Protege Undergraduate Research Program
The protege program was started by the College of Engineering and Applied Science during the summer of 2013. The goal of the program is to make students aware of opportunities for careers in research. These opportunities are for outstanding first-year students to work with leading CEAS research faculty in their faculty labs during the summer after their first year in CEAS.
The program initially included five to six students per year but in 2016, the program was expanded to eleven students and included research at industrial and governmental partners. The program has been administered by a committee of senior faculty members (J. Boerio, T. Mantei, and R. Huston)
Learn more about undergraduate research
For more information concerning Protégé, contact:
Dr. James Boerio, f.james.boerio@uc.edu
Benefits
The Protege program enhances the student experience by having them learn to conduct research, work as part of a team, keep laboratory notebooks, write reports, and make presentations.
In addition, students are paid at the rate of $15.00 per hour for 40 hours of work each week between 12-15 weeks in the summer. The length of the program is at the discretion of the mentor, 12 week being the minimum.
The opportunity allows students to determine if they wish to pursue a co-op position and career in research. At the same time, participating industrial and governmental partners have an early opportunity to recruit highly talented and motivated student researchers.
Selection Process
Each spring, first year CEAS students who performed at a high level during the autumn semester are identified by a CEAS faculty committee. Most participating students have grade point averages of 3.75. Students are interviewed to determine interest in research careers and availability to work in Cincinnati or at the location of an industrial or governmental partner over the summer.
Interviews are conducted by the CEAS faculty committee and by participating partners in which a broad groups of students are selected.
Expectations
- Report for work at appropriate times
- Learn as much as possible about your project
- Show interest in and enthusiasm for the project
- Do good research
- Participate in professional development workshops offered by UC
- Submit a short mid-summer report
- Submit a short final report
- Participate in final symposium
- Don't work more than forty (40) hours per week!
- Contact Dr. James Boerio, (f.james.boerio@uc.edu) if there are any problems
2025 Research Projects
Research projects that are involved with the Protege program must advance the state of knowledge or understanding in a particular field. Students do not usually define the project and are defined by the mentors. These are not make-work projects. Protege students usually contribute to an important, larger project that are usually funded by some agency or industry that are important to the company. Students and mentors must agree on the project.
Unmanned Aerial Vehicles (UAVs) or drones have generated a lot of interest recently among the research community due to their potential to revolutionize some of the applications in civilian domain such as emergency management, law enforcement, infrastructure inspection, precision agriculture, package delivery, and imaging/surveillance. While there has been a lot of progress in drone applications in outdoor environments, indoor usage of drone has been limited even though there are several applications such as warehouse management and indoor emergency response. The objective of this project is to build a drone that can deliver telehealth services to people inside their homes. Operation of drones in indoor environment is particularly challenging due to several reasons including loss of access to GPS information, and proximity with obstacles and humans. For safe operation of UAVs in indoor environment, some level of autonomy is needed to allow UAVs to avoid collisions and carry out basic maneuvers without any assistance from humans. Incorporating autonomy in drones operating in indoor environment is often challenging due to the fact that positional feedback from GPS is intermittent or unavailable. The UAV needs to solve the problem of localization, i.e., finding its position and orientation using onboard sensors such as vision, laser, or other proximity sensor such as ultrasound sensors, via a process called Simultaneous Localization and Mapping (SLAM). Furthermore, the UAV should be able to use its positional estimate to perform navigation in a precise manner to enable safe operation. The objective of this project is to develop hardware and software means to carry out the process of SLAM and autonomous navigation of UAVs in indoor environments. To alleviate the safety issue arising due to operating close to humans, a prototype is being developed that can be remotely controlled via cellular network. This prototype will have inbuilt intelligence for obstacle avoidance, autonomous landing, communication delay, and lost communication. Apart from the hardware and software components, the project would involve carrying out flight tests in indoor and outdoor environments. This is a part of ongoing National Science Foundation funded project that involves researchers from multiple disciplines including College of Nursing and College of Allied Health Sciences. The student will be working in a multidisciplinary team of researchers and graduate students.
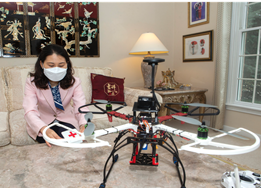

The COVID-19 pandemic is one of the gravest global public health and socioeconomic challenges of our times. While, currently, apparently on the wane, the havoc continues in successive waves driven by viral and the challenges associated with of effective vaccination and herd immunity. Hence the focus has shifted from elimination of COVID-19 to planning for management of future outbreaks. Moreover, epidemiological consensus underscores the inevitability of other future epidemics triggered by novel pathogens. Mitigation of such epidemic spread caused by pathogens is achieved via Non-Pharmaceutical Interventions (NPI) (e.g., social-distancing, use of masks) and Pharmaceutical Interventions (PI) (e.g., vaccines). NPI play a crucial role, particularly during the early stages of an outbreak since developing PI to counter a new pathogen inevitably takes time and hence costs millions of human lives. However, the efficacy of such interventions is critically dependent on the accuracy of scalable, predictive mathematical and computational models of infection spread that can be updated in real-time based on evolving spread data. Overall objective of this project is to create new scientific pathways in epidemic modeling and predictive analysis that will synergistically integrate: first principles mechanistic modelling of infection spread, characterization of the effects of uncertainties driving an epidemic spread using rigorous stochastic analyses, model validation using empirical data, and new knowledge of epidemic dynamics thus created to develop a control-theoretic architecture to analyze PI and NPI countermeasures. This will be done using mathematical framework of partial differential equations for modeling, control-theoretic framework for mitigation of epidemic spread, and validation/verification using COVID-19 data.
This is a multi-university National Science Foundation sponsored project that involves cross-disciplinary research comprising engineering and epidemiology. The undergraduate researcher will be working with the team in development of Artificial Intelligence based tools to learn parameters of model from data to improve the prediction efficacy.
Skills required: Proficiency in programming language such as Matlab and/or Python
Training provided:
1. Computational/numerical methods
2. Programming using open source AI/ML tools
3. Data collection, organization, and processing
4. Cross-discipline collaboration and collaboration with graduate students
5. Research publications in conferences and/or journals
· Neuromorphic Computing and Artificial Intelligence: Artificial Intelligence (AI) has caught significant research attention. However, AI algorithms are compute resource intensive. Therefore, much emphasis has been devoted on developing specialized neuromorphic System on Chip (SoC) for accelerating AI recently. Some examples of these neuromorphic-SoC include Google’s TPU, Intel’s Nirvana and Loihi, and IBM’s TrueNorth. In spite of these significant advances, the performance of these processors are limited by the lack of novel reconfigurable memory devices that can mimic the adaptive characteristics of biological synapses. MIND lab researchers have invented new type of artificial synaptic devices that can provide lucrative options for neuromorphic SoC. The student working on this project will work on this cutting-edge technology and develop neuromorphic SoC utilizing these novel memory devices. The student will perform the following tasks:
- Testing and Modeling of Synaptic Memory Devices in Verilog/VHDL
- Modeling and simulation of neural circuit modules
- Implementation of learning algorithms and performance evaluation of this novel neuromorphic SoC
- Publication and presentations.
- Training data collection on drones fitted with cameras and multiple sensors.
Trusted and Secured Microelectronics Hardware: Due to complex supply-chain of microelectronics integrated circuits (IC) design and fabrication, hardware security has emerged out to be one of the prime concerns. This project seeks to develop novel ways to design and fabricate secure microelectronics circuits using emerging nanoelectronics logic and memory devices. The students will be involved in the design of ICs, simulations, fabrication, and testing. A fundamental question we will try to answer is how can design itself be made more trust-worthy and resilient? Can emerging nanoelectronic memory and logic devices offer any inherent benefit in this area?
- Advanced Semiconductor Logic and Memory Devices: With the end of Moore’s Law of conventional transistors scaling, novel logic and memory components are needed to address the demands of the next generation of computing. This project will train students on fabrication and testing of next generation of logic and memory devices. DNA based computing and data storage approaches will also be explored.
PI Dr. Rashmi Jha, who is the director of MIND lab, has more that 15 years of experience in the areas of nanoelectronic logic and memory devices, neuromorphic devices, circuits and architecture, and microelectronics in industry (IBM Research) and academia. MIND lab provides an excellent research environment to the students and is currently supporting 5 PhD, 5 MS, 4 UG students. The students will work in the team of graduate, and undergraduate students, and PI in these stimulating research areas. Students will be mentored via weekly group meeting and one-to-one interactions with PI and encourage to publish work and attend conference.
Dr. Hoilett is an Assistant Professor of Biomedical Engineering. He graduated from Purdue University in 2021 with a PhD in Biomedical Engineering and from Vanderbilt University in 2014 with a Bachelor of Engineering also in Biomedical Engineering. His academic interests involve developing wearable sensors for mobile health platforms and engaging engineering design activities for undergraduate and graduate students. He has several years of experience with analog circuit design and embedded systems. His previous work includes developing a wearable opioid overdose monitor for substance use disorder patients and developing an impedance analyzer for a microfluidic blood-brain barrier model among other projects. On the education side, he has developed several lab activities for first year and junior level Biomedical Engineering students. He was instrumental in developing the Milestones Program at Purdue, a certificate-granting series of workshops providing students professional engineering skills utilized in rapid-prototyping and industrial applications. At the University of Cincinnati, Dr. Hoilett’s lab will continue developing low-cost diagnostics and sensors for improving patient-care both in high-resource and low-resource settings, tackling healthcare disparities and unmet clinical needs worldwide.
Babies born premature (approximately 10% of the population), can experience a range of neurological, ocular, respiratory, gastrointestinal and musculoskeletal impairments. For these infants, proper nutrition in the early stages of life is crucial to achieving short-term clinical milestones and long-term growth and development. The best nutrition source for premature newborns to achieve these goals is breastmilk but preserving the nutrient benefits of this complex liquid biologic tissue can be very challenging.
It has been established that there is substantial adsorption of macronutrients to the surfaces of containers, feeding tube lines, and other interfaces, a process that often reduces the total nutrient delivery to the infant. For donor milk, the nutritional loss is especially severe because there are a considerable number of steps between expression of the breast milk and its delivery to the infant. These include, pasteurizing, screening, pooling, freezing, transporting, thawing, preparing, and administering the milk. Each step offers the potential for macronutrient loss, and it is particularly detrimental to infants that require tube feeding. In order to improve clinical outcomes for at-risk infants, it is critical to ameliorate this macronutrient loss.
While others have examined single components of the milk transfer system, we propose to apply a systems-level analysis to the entire milk transfer system and identify the points where macronutrient loss is the greatest. We will then use a patented technology to develop a polymer-based lining material that will prevent macronutrient adsorption and significantly improve nutrient delivery to infants, especially those in the NICU. This project’s specific aims are:
Aim 1: Characterize the amount of macronutrient loss through current collection, storage, and handling methods utilized in the processing of freshly expressed and frozen (mother’s and pasteurized donor human milk (PDHM)) and determine critical points of loss within the system.
Aim 2: Demonstrate the ability of pharmaceutical grade polyethylene glycol (PEG), a strongly hydrophilic molecule, and calfactant (trade name Infasurf), a naturally derived surfactant, to significantly decrease nutrient loss from polymers in the milk handling system.
Aim 3: Demonstrate the successful translation of nutrient-protecting coatings in a prototype milk-transfer system.
This project is in collaboration with Cincinnati Children’s and Professor Eric Nauman’s Human Injury Research and Regenerative Technologies (HIRRT) lab.
Replace this text component with your accordion's content.
Angelman syndrome (AS) is a neurogenetic syndrome associated with severe developmental and intellectual disability. Symptoms of AS include very limited speech, difficulty sleeping, and poor motor function. AS is caused by a mutation or deletion of the UBE3A gene on the maternal chromosome 15 and is typically diagnosed in the early childhood period using genetic testing. At present, there is no cure for AS. Treatment is focused on supportive therapies and pharmaceuticals to manage seizures and reduce behavior problems. The AS community is motivated to find a cure, and several major gene therapy trials are underway to reduce or potentially reverse symptoms.
Despite increased investment in clinical trials, functional outcomes that impact the lives of people living with AS and their families remain widely variable. A major barrier to clinical trials is the lack of available outcome measures suitable for AS. Wearable devices that monitor physiological and behavioral output are promising solutions because they provide objective metrics of physiological function without requiring verbal or motoric input from the patient. However, typical wearable devices in form factors such as smartwatches and headbands are often not tolerable by AS patients. Using input from AS caregivers from extensive focus groups (N = 8) conducted by our research team, we have designed MyA, a biometric vest that will measure several key signals relevant to AS (heart rate, respiration, vocalizations, temperature, and sleep), while meeting the unique sensory and tactile needs of the AS population. For our preliminary developments, we sewed conductive fabric and conductive silicone into separate commercially available athletic vests composed of primarily nylon, polyester, or polyamide. Our preliminary measurements of the electrocardiogram demonstrate the ability to capture key biosignals using our textile prototype. We were able to measure heart rate from the electrocardiogram within 2.4 beats per minute of a commercially available reference chest strap heart rate monitor with high correlation between the two devices (r = 0.88, p < 0.05).
For the proposed project, the student researcher will work closely with a senior member of the lab to integrate audio and video capabilities into the vest. Audio and video are important behavioral inputs that allow us to understand levels and styles of communication in people with AS. We would also like to understand how people with AS interact with others and their environment, and vice versa. The student will work with the senior member of the lab to validate each sensor on the benchtop and develop code that can be integrated seamlessly into the biosensor prototype.
This project is in collaboration with Purdue University Department of Psychological Sciences.
Replace this text component with your accordion's content.
Worldwide, premature birth accounts for 30% of all neonatal deaths in children under the age of five. Neonatal hypothermia is one of the most common complications of premature birth as newborns are unable to regulate their body temperature. Hypothermia is an especially devastating complication of premature birth in low-resource settings. Over 80% of deaths due to premature birth occur in low and middle-income countries (LMICs), due to a lack of access to incubators that are critical for managing hypothermia. Furthermore, LMICs lack the necessary tools to regularly monitor the baby’s vital signs, which is critical for managing complications due to premature birth. Deaths from sudden infant death syndrome (SIDS) and accidental suffocation are silent and go unnoticed without continuous vital sign monitoring. Kangaroo mother care (KMC) is a proven intervention for combating neonatal hypothermia and involves skin-to-skin contact between the caregiver and the newborn. However, KMC places high demand on caregivers, and leaves newborns with no protection when caregivers require a break to care for themselves. Furthermore, it is very difficult to measure a baby’s vitals during KMC as the baby is swaddled tightly to the caregiver and is not accessible. As a result, KMC still leads to deaths due to SIDS or accidental suffocation as the caregiver is unaware of the baby’s vitals during KMC.
Our patented device, NeoWarm, is a disinfection wipe-friendly infant carrier that serves the need for thermal management and vital signs monitoring of premature infants during and in between KMC. NeoWarm has integrated fabric heating pads that generate heat from a lightweight, rechargeable, portable battery pack in similar fashion to an electric jacket. NeoWarm also includes sensors for heart rate, respiratory rate, blood oxygen, and temperature, to monitor the infant’s key vital signs to detect signs of hypothermia and other complications such as apnea or SIDS. Given the strength of our benchtop and preclinical studies, our present study aims to validate NeoWarm in a clinical setting with human babies. To accomplish these goals, we have the following aims:
Aim 1 (Electronic Circuit Design Aim / Option #1 for student): Develop a the second-generation NeoWarm device with integrated sensors for heart rate, respiration, blood-oxygen, and temperature. The student will help develop a professional-grade printed circuit board as well as firmware that will simultaneously track each physiological signal of interest using a microcontroller and send the resulting data to a previously developed smartphone application using Bluetooth Low-Energy.
Aim 2 (Microbiology Aim / Option #2 for student): While NeoWarm has the potential in reducing neonatal hypothermia, its role as a potential fomite is yet to be determined. Neonatal care settings pose a heightened risk of neonatal sepsis due to the vulnerable population of preterm infants with underdeveloped immune systems. Pathogens such as Enterococcus faecium, Acinetobacter baumannii and Pseudomonas aeruginosa are implicated in neonatal sepsis. Similarly, indicator organisms, such as Escherichia coli are noteworthy in neonatal sepsis due to their association with contamination and poor infection control practices in healthcare settings. To further ensure the safety of the NeoWarm prior clinical trials, a comprehensive microbial risk assessment is imperative.
The interested student can choose to work on Aim 1, Aim 2, or both.
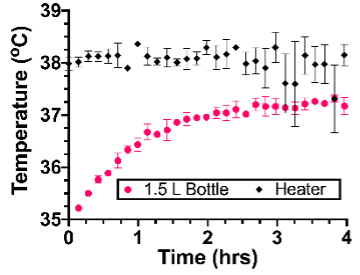
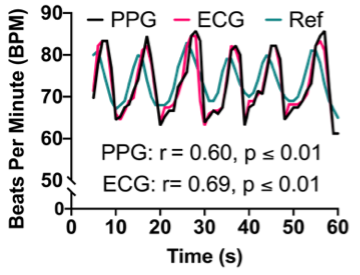
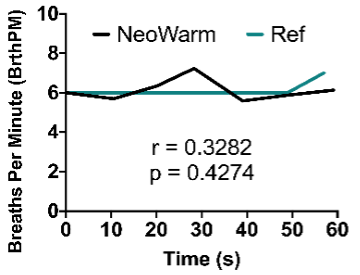

Premature infants, especially those born over 10 weeks early, are at greater risk for intraventricular hemorrhage (IVH), a condition characterized by bleeding of the ventricles due to underdeveloped blood vessels. This risk is heightened in very low birth weight (VLBW) neonates, who typically have a gestational age of less than 30 weeks and weigh less than 1.5 kg. IVH is classified into four grades. Grades III and IV are the most severe and can potentially lead to long-term developmental and motor issues, as well as an increased mortality. Transport is a known risk factor for developing IVH. However, many premature infants must be transported due to their need for specialized neonatal intensive care that may be unavailable at their birth facilities. Studies show that VLBW neonates born outside of tertiary care centers (outborn) and transported to specialized facilities have a higher incidence of severe IVH compared to those born in specialized care centers (inborn). The increased risk of developing IVH due to transport is potentially linked to the forces experienced during transport, including whole-body vibrations, translational forces, rotational moments, and excessive sound. As a result, many have endeavored to characterize these distressing forces and develop novel techniques to reduce them to acceptable levels. Some studies have suggested using a foam, air, or gel mattress inside the isolette to absorb the forces inside the isolette; however, the results were not statistically significant. As a result of this unmet clinical need, our goal is to mitigate the vibrations and noise levels experienced during all forms of transport (ground, fixed-wing, and rotary-wing), towards decreasing the incidence of IVH and improving the outcomes for premature infants worldwide.
In our preliminary work, we have documented the mechanical vibration and sound exposure experienced by a neonatal manikin during ground transport in a Type 1 ambulance provided by Cincinnati Children’s Hospital and Medical Center (CCHMC). We used 14 triaxial accelerometers, referred to as “Peapods,” and two sound level meters. The Peapods were placed on the manikin, isolette, and throughout the interior of the ambulance (Fig. 1A). The sensor on the manikin was placed on the manikin’s forehead (Fig. 1B and 1C). One sound meter was placed inside the isolette, while the other was placed on top of the isolette. The ambulance drove for 25 minutes with a mix of highway and city miles, and briefly activated the siren to simulate authentic transport scenarios. Our results indicated that the manikin experienced forces exceeding the recommended “comfortable” 0.032 g limit for the entire duration of the simulated transport event. The average noise level inside the isolette was 63.4 dBA, which is 18.4 dBA higher than the level recommended by the AAP. Given the strength of our preliminary data, our current study aims to characterize the vibrations and noises experienced during ground transport in a Type II ambulance, as well as during fixed (ambulance) and rotary wing transport (helicopter). We will then evaluate methods to mitigate the mechanical vibrations and noise levels experienced during all forms of transport. We will accomplish these goals with the following specific aims:
Aim 1: Determine forces and noise levels experienced by a neonatal manikin during a non-ambulatory transport event in a type II ambulance, during fixed-wing transport, and during rotary-wing transport. Aim 2: Determine the vibration dampening capabilities of memory foam. Aim 3: Determine the optimum soundproofing material for the transport isolette per weight of material.
Intra-abdominal hypertension (IAH) and abdominal compartment syndrome (ACS) are comorbid conditions that could result in low perfusion to the abdominal area and lower extremities, consequently negatively affecting oxygen delivery to organs, ultimately leading to organ failure, and death. Incidence rates of ACS in the literature vary, but some reports show rates as high as 20%. IAH and ACS are indicated primarily by intra-abdominal pressure (IAP) with IAH defined as IAP greater than 12 mmHg and ACS defined as IAP greater than 20 mmHg. This is often, but not exclusively, seen in neonates with necrotizing enterocolitis (NEC) (inflammation or perforation of the intestines). In neonates, even slightly elevated IAP of 5 mmHg, well before the threat of ACS, can lead to extreme discomfort and difficulty feeding as additional fluid introduced to the abdominal area from feeding further elevates IAP, dangerously progressing the neonate to ACS. Disrupting an infant’s nutritional intake is especially detrimental at this stage in life where regular feeding schedules must be maintained to help babies grow and develop. The gold standard of quantitative IAP measurements is a peritoneal catheter; however, catheterization is invasive and very risky and may require sedation or paralysis. As a result, physicians rely on palpation to monitor IAP. However, studies have shown that palpation is unreliable with up to 60% of patients being misdiagnosed. Given the need for monitoring IAP to prevent ACS, support regular nutrition, and detect NEC, the difficulty in monitoring IAP using a catheter, and the unreliability of palpation, there remains a need for a simple, noninvasive method of measuring IAP in neonatal populations.
Abdominal wall tension (AWT) has shown potential as a non-invasive, indirect measure of IAP, being previously validated in adults. AWT can be measured with a force sensor as the sensor lightly presses into the abdomen (~5 mm depth) and is similar in principle to the palpation method but provides objective measures of force instead of the “sensation of force” as with palpation. Previous studies have correlated AWT to IAP in adults, but not in neonates. Given the differences in skin and soft tissue elasticity of neonates compared to adults, which could impact the relationship between AWT and IAP, it is necessary to explicitly characterize the relationship between AWT and IAP in the neonates to assess whether AWT is a proper indirect measure of IAP in this population. This research aims to demonstrate that AWT is a safe, non-invasive, indirect measure of IAP in neonates and can be leveraged to decrease the incidence of IAH, ACS, and NEC, as well as support clinical decision-making regarding nutrition.
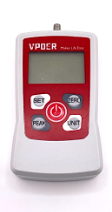
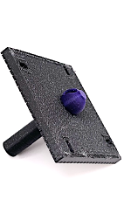
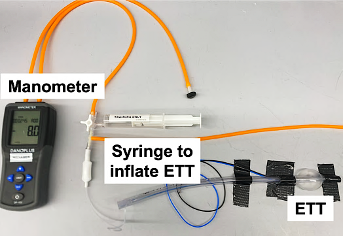
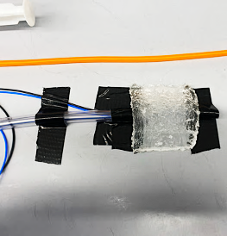
Post-operative monitoring has many difficulties since medical professionals can't actively track their patient's health. Patients who have undergone pancreatic surgery for cancer have a high readmission rate because of the complexity of the surgery. Pancreatic cancer surgery can entail the removal of parts of the small intestines, part of the bile duct, gall bladder, lymph nodes, spleen, parts of the pancreas, and even sometimes the whole pancreas. Patients who have gone through pancreatic cancer surgery are at higher risk of leaking from the reconnection of organs, infections, internal bleeding, and problems digesting food. These high-risk factors are why post-operative monitoring is essential in reducing the chances of readmission by catching issues early. Studies have shown the benefits of wearable devices by predicting the possibility of readmission by monitoring health data such as steps, heart rate, and sleep. Still, they have had difficulty in missing data due to improper adherence, running out of battery, or complications connecting to phones for data storage. Modern-day wearable devices can also be complicated for elderly patients because of their various applications or uses. There are also issues with clarifying FDA-approved settings within certain smartwatches. This research aims to develop a simple, easy to use wearable for frustration-free post-op monitoring of pancreatic cancer patients.
Replace this text component with your accordion's content.
We are all familiar with the sight of an athlete experiencing a severe blow to the head and being unable to stand or walking shakily back to the sideline. In those instances, it is clear that the athlete has experienced a “concussion.” Concussion, as defined by the Guideline Development Subcommittee of the American Academy of Neurology, is a syndrome of biomechanically induced alteration of brain function potentially affecting memory, orientation, and state of consciousness and is the most common type of mild traumatic brain injury. Despite early work suggesting that concussion symptoms were directly correlated with the magnitudes of singular impacts, a more complete analysis of the data has made it clear that an impact threshold does not exist. In fact, the deleterious consequences of repetitive head impacts or sub-concussive blows can accumulate over time, causing tissue level damage that both increases susceptibility to later head impacts, and generally increases the volume of damaged brain tissue.
While numerous attempts have been made to design sensor systems to measure head impacts, including in-helmet systems, wearable accelerometers, and even mouthguards, they only quantify risk of injury and even so with varying accuracy. Additionally, these sensors do little to encourage better technique. Recent work demonstrating that improved technique decreases an athlete’s exposure to head impacts suggests that the best intervention is one that helps coaches better prepare their athletes for practices and games. The goal of this project is to develop a system that mitigates head injury by tracking the force of each hit and provides a video-based tool that will allow coaches to teach better technique.
The student will work with a senior member of the Hoilett and Human Injury Research and Regenerative Technologies (HIRRT) labs to develop a miniaturized device that combines high-impact accelerometers, GPS, and Bluetooth capabilities into a single, discreet wearable. The wearable will track the force delivered by repetitive head impacts, map the location of these forces in real-time on a practice field, and relay this information back to a bay station that can be monitored by coaches and athletic training staff.
Electrically driven fans and compressors are finding applications in everything from aircraft propulsion down to hand dryers, vacuums, and power tools. This research project will be focused on studying the noise generated from an electrically driven fan with opportunities to assist simulation and experimental efforts.
Research tasks may include:
- Develop a reduced order model for fan performance and acoustics of a ducted fan
- Computational Fluid Dynamics and Aeroacoustics simulations of a ducted fan
- Meshing and simulating fluid flow in a ducted fan configuration and ANSYS Fluent
- Investigating the capability of aeroacoustic modules in ANSYS Fluent
- Developing an experimental setup to measure the acoustics and performance of a ducted fan.
- Design and fabrication of hardware to support measurements
- Development of data acquisition software to support measurements
Hypersonic flight involves flying at Mach numbers greater than Mach 5. The propulsion systems to propel aircraft at these speeds have multiple shock wave systems for compressing the incoming air for achieving combustion. We have designed and fabricated a new high-speed wind tunnel facility called the Hypersonic Propulsion Wind Tunnel (HPWT). The facility will have full optical access in the test section to enable advanced optical diagnostics internal to the propulsion flowpath with the ability to control backpressure which simulates changing conditions during hypersonic flight. The facility will include instrumentation such as pressure, temperature, and flow measurement that needs to be integrated with the wind tunnel. Additionally, a data acquisition and control code needs to be written for operation and control of the facility and recording data during testing.
This project will involve assisting with:
1) Installation of the wind tunnel instrumentation and control hardware
2) Development of software for wind tunnel control and data acquisition
3) Assisting with experimental measurements on the HPWT and a supersonic cavity flow experiment
Aeroacoustics is the study of noise generated from aerodynamic phenomena. A common source of noise, aerodynamic turbulence, is found everywhere from nature to aircraft systems. This project will involve measuring the turbulent flow over a human head and human ear across a range of conditions in a low-speed wind tunnel. This project will analyze detailed measurements of the turbulent flow, realistic acoustics in the human ear, and study flow control to reduce turbulence noise on the human ear to improve audibility in windy environments.
Initial acoustic and flow measurements have been conducted on the ear installed in a 3D-printed model head. The student involved will
1) Analyze the velocity field data already acquired
2) Develop designs for controlling the flow in the vicinity of the ear to reduce noise.
3) Acquire additional acoustic and flow measurements with the flow control devices applied will be conducted to characterize the effectiveness and change in the acoustic source field.
Peripheral nerve injuries impact millions of Americans each year with many more living with the effects of traumatic nerve injuries. In severe peripheral nerve injuries, nerve pathways, connections, and the extracellular matrix (ECM) tissue surrounding nerve that lead to the sensory or motor targets are damaged. If the injury gap is larger than approximately 2 centimeters, functional recovery is extremely limited and no adequate therapies are currently available for doctors. This deeply impacts the quality of life due to the loss of connection between the central nervous system and the body’s extremities. Neurons do not have the ability or needed signals from the damaged ECM surrounding the injury site to allow guided growth of axons across the injury space. Therefore, this project will address the urgent need to engineer new biomaterials that give the proper electrical, physical, and chemical signaling to cells and neurons for guided nerve regeneration and provide functional recoveries in traumatic nerve injuries. This will be accomplished by engineering biomaterials that cells will attach to (Figure 1A,B) and possess the proper physical, electrical, and chemical signals in order to direct cell alignment and growth. We will develop these biomaterials to deliver defined, tunable signals to the cells to elicit the desired cellular outcomes (Figure 1C,D). It is hypothesized that the biomaterial, in combination with relevant cells and ECM, will functionally bridge the injury gap to restore function to injured tissues.
(A,B) Scanning electron microscopy image of electrospun PVDF polymer of defined chemical, physical, and electrical properties with Schwann cells growing on fibers. Confocal microscopy showing (C) Schwann cells in a 3D z-stack projection on PVDF and a (D) maximum intensity image showing alignment of cells on fibers.
The vascular smooth muscle cells (VSMCs) that comprise the medial layer of arteries exhibit two distinct phenotypes: contractile and synthetic. Contractile VSMCs regulate blood pressure in the artery but can dedifferentiate into the synthetic phenotype in response to injury. We are hypothesizing a potential third phenotype of VSMCs initiated by mechanical strain caused by hypertension, known as the silent killer. We propose that this third phenotype happens through the Wnt signaling pathway as VSMCs become osteoblast-like cells and deposit mineral into the arterial extra cellular matrix. This project would provide new knowledge by confirming the continued plasticity of VSMCs caused by mechanical strain activating the canonical Wnt signaling pathway. By understanding the signaling pathway associated with this phenotypic modulation of VSMCs, we could work to develop targeted therapeutics to treat vascular calcification at the cellular and molecular level.
My research group has optimized and validated an in vitro model approach for inducing phenotypic modulation and calcification, we studied the calcium content in primary aortic smooth muscle cells. Inorganic sodium phosphate was used because it is known to induce phenotypic modulation and calcification in vascular smooth muscle cells. The calcium content for the phosphate-treated groups was significantly increased compared to the control groups. To further confirm the model’s ability to induce phenotypic modulation and calcification, we performed scanning electron microscopy (SEM) and energy-dispersive x-ray spectroscopy (EDS) to visualize and quantify the calcification present in the samples [Figure 1]. Given our ability to induce phenotypic modulation through phosphate supplemented media and literature hypothesizing this phenotypic switch occurs through the canonical Wnt signaling pathway, we want to examine this pathway as a therapeutic target. This protégé project would involve confirming the role of Wnt signaling in synthetic vascular Smooth muscle cells.
Experimental Plan:
1) Induce smooth muscle cells into a synthetic phenotype.
2) Examine the stability of the synthetic phenotype.
3) Confirm Wnt signaling as essential for phenotypic modulation.
Training Provided:
- Polymer synthesis
- Materials characterization
- Aseptic technique
- Cell culture
- Potential for research publications and presentations at local and national conferences
The addition of inorganic phosphate significantly induced phenotypic modulation and calcification as compared to controls in calcified cells over 7 and 14 days (p<0.05). SEM images demonstrate the increase in mineral nodule formation in (Fig 1C & 1D) calcified cells over controls (Fig 1A & 1B). EDS analysis confirmed the presence of calcium and phosphorus ions in the mineral nodules. Figure 1C
Project description and scope:
Electroplating process is used to plate Zinc – Nickel coating on 300 M steel. Selected student will assist graduate students in conducting electroplating experiments. Specific activities include:
a) Data collection: Data from experiments include SEM images, process parameters, electrolyte composition, and data from literature relevant to experiments.
b) Generative Modelling: Developing generative models to discover new electrolytes based on experiments and data from literature. Analyze those models, decide how to iterate through various modeling approach according to output. Students are expected to use this electrolyte compositions to do experiments and compare coating quality
Selected student will gain exposure to:
- Conducting a literature review
- Hands-on experiments with an electroplating setup and hardware
- Analysis of experimental results
- Exposure to machine learning
- An excellent opportunity to exercise your initiative, creativity, critical thinking, scientific judgment, scientific knowledge, problem solving, and teamwork skills
The Protégé student will be paired with a Ph.D. student and assist in the research and development of continuous electrochemical aptamer biosensors for chronic disease monitoring. Current focus is on developing sensors related to heart failure, insulin for diabetes patients, and cortisol for stress monitoring. The sensors are adapted to work with existing continuous glucose monitor wearables (also known as ‘CGM’). The work involves basic wet-chemistry, device fabrication, electronic testing, and data analysis/presentation. Students begin with gold electrodes, and the place down special DNA-based chemistry (aptamers) that can react with and measure the molecule to be measured, providing an electrical signal that can then be reported on a smart phone to the user. A goal for the Protégé includes co-authorship on at least one publication resulting from the work with the Ph.D. student.
Many people are dissatisfied with their voice, but relatively few are aware that voice can be changed through repetitive practice. Such practice is often provided by speech-language therapists, but they are expensive and often inaccessible. Our group thus previously developed a prototype of free web-based voice training software for transgender people, and the Figure below shows an example of pitch exercises available through the software: matching a sequence of five pitch values while speaking a 5-syllable word. In this project, the student will work on expanding the software to new target applications (e.g., making voice less nasal) and adding new features (e.g., long-term performance tracking). The work is expected to involve a combination of design, web development, signal processing, and human subjects testing.
Protege Mentors
- All mentors have extensive research programs
- All mentors are known for working with young researchers
- Faculty usually have extensive research programs
- Have graduate students that help mentor Protege students
- Industry mentors have group members that help mentor students
Protege mentors are expected to work with beginning students to develop their research project. Mentors should provide students with background information about the project and be able to answer the following:
- What is the goal?
- What approach is envisioned?
- What results are being sought?
Protege mentors should provide resources required to accomplish the project and be available to provide ongoing advice on the project. They should personally spend about three (3) hours per week with the student.
Contact Us
F. James Boerio
F. James Boerio received the B.S. Degree in Physics from Case Institute of Technology and the M.S. and Ph.D. degrees in Macromolecular Science from Case Western Reserve University. He was appointed as Assistant Professor of Materials Science in the Department of Materials Science and Engineering at the University of Cincinnati in 1970 and promoted to Professor of Materials Science in 1977. He served as Interim Head of the Department of Materials Science and Engineering during 1991-92 and again during 2003-04. Dr. Boerio was appointed Head of the Department of Engineering Education on January 1, 2008 and currently serves as Interim Head of the School of Engineering Education. His educational research interests include the effect of factors such as institutional infrastructure, active learning, and peer-level tutoring on learning in engineering. Dr. Boerio is also interested in developing professional skills, including communication, problem-solving, and teamwork, in beginning engineers.
Dr. Boerio is a member of numerous technical societies, including the American Society for Engineering Education, American Physical Society, American Chemical Society, Materials Research Society, Society for Applied Spectroscopy, and American Vacuum Society. He served as President of The Adhesion Society from 1992-94 and currently serves as an Associate Editor of The Journal of Adhesion.
Dr. Boerio was recognized as an outstanding teacher by the Engineering Tribunal in 1983 and as "Professor of the Year" for 2002-03. He received the College of Engineering Research Award in 1989 and the “Dean’s Award for Educational Innovation” in 2001. Dr. Boerio was elected a Robert L. Patrick Fellow of The Adhesion Society in 1997 and received the Adhesion Society Award for Excellence in Adhesion Science, sponsored by 3M, in 1999.