Protege Undergraduate Research Archives
2019 Protege Research Symposium
Emeritus Professor James Boerio making opening remarks at the 2019 Protege Symposium.
2024 Undergraduate Research Topics
The usage of Robots for surgery has increased substantially in recent years and involves the use of robotic systems to perform surgical procedures. The primary aim is to enhance the capabilities of surgeons, providing greater precision, flexibility, and control. Some common applications of robotic surgery include cardiac surgery, gynecological surgery, urological surgery, colorectal surgery, head and neck surgery, orthopedic surgery, ENT (ear, nose and throat) surgery, neurosurgery, and pediatric surgery (see few examples in Figure 1).
Specifically, our team has funding secured to explore extension of robotic surgery for space applications as NASA ventures towards extended crewed Mars missions. Figure 2 provides an illustration of the main issues associated with surgery beyond low earth orbit.
Research Tasks Proposed: (1) Acquiring an understanding of a robotic surgery control systems (literature review); (2) Introduction to Fuzzy Logic Systems and MATLAB toolbox; (3) Conventional (Linear Quadratic Regulator) Control and Fuzzy Logic controllers and MATLAB implementation/simulation; (4) Application to a idealized rubric surgery model and sensitivity studies; (5) Potential for research publications and presentations at the local and national levels.
Research Location: This research project will be completed in Prof. Cohen’s AI Bio Lab at Digital Futures, Suite #300.
A transformational era in flight is upon us with the increased ubiquity of Unmanned Aerial Systems (UAS), in particular, the burgeoning interest in Unmanned Aerial Mobility (UAM) for mobilizing cargo and passengers. While the precise application and market for these vehicles is still developing, there will definitely be more of these UAM vehicles flying in and around populated areas. One of the key enabling factors for realizing the quantity and frequency of flights that are envisioned will be the noise levels produced by UAM as they operate in populated areas. In order to develop low noise UAM, air vehicle designers need data, design tools, and technology to enable the development of quiet vehicles from conceptual design stage all of the way through detailed design. Currently, there is a lack of data and capability for predicting the noise produced by UAM until millions of dollars have been spent to design, fabricate, and fly the vehicle. This is why acoustics needs to be factored into the earliest stages of conceptual design in order to develop a vehicle that achieve the quietest design possible.
Current research projects in this area may include:
1) Experimental acoustic and flow field measurements of a 6-bladed propeller
2) Development of LabVIEW code for control and data acquisition
3) Working with acoustic prediction tools like NASA ANOPP2 or Volpe AAM to predict noise from a propulsion system or flight vehicle
4) Develop data processing software to synthesize acoustics and flowfield data to provide data-driven insights into the dominant noise mechanisms
This research will characterize a boundary layer downstream of high-pitch fluidic injectors that inject flow into a boundary layer at shallow angles relative to the freestream. The focus of the research will be characterizing the downstream boundary layer health in terms of the boundary layer thickness, displacement thickness, momentum thickness, and shape factor. The three-dimensionality of the boundary layer will be measured to characterize the spanwise effects on the boundary layer. The goal of this research is to study the fundamental physics of shallow wall jets and their impact on the boundary layer health to identify promising designs for decreasing the local momentum deficits in boundary layers. This research will be conducted in a subsonic wind tunnel up to Mach numbers of 0.3.
Research tasks will include:
1. Design and additively manufacture injection systems
2. Slot and multiple jet array
3. Exploring alternative measurement techniques such as Infrarerd Imaging or PIV
Hypersonic flight involves flying at Mach numbers greater than Mach 5. The propulsion systems to propel aircraft at these speeds have multiple shock wave systems for compressing the incoming air for achieving combustion. This presents many challenges such as energy losses due to shock-boundary layer interactions. Additionally, achieving ignition and sustaining combustion at these conditions is extremely challenging. A new facility is currently being designed and developed with planned fabrication in the summer of 2022. The facility will have full optical access in the test section to enable advanced optical diagnostics internal to the propulsion flowpath with the ability to control backpressure which simulates changing conditions during hypersonic flight.
This project will involve assisting with:
1) Development of control systems for wind tunnel operation
2) Development of software for wind tunnel control and data acquisition
3) Installation of wind tunnel in the Rhodes 300 lab including instrumentation, control systems, data acquisition systems, and fluid systems (tubing, piping, etc.)
Aeroacoustics is the study of noise generated from aerodynamic phenomena. A common source of noise, aerodynamic turbulence, is found everywhere from nature to aircraft systems. This project will involve measuring the turbulent flow over a human head and human ear across a range of conditions in a low-speed wind tunnel. This project will analyze detailed measurements of the turbulent flow, realistic acoustics in the human ear, and study flow control to reduce turbulence noise on the human ear to improve audibility in windy environments.
Initial acoustic and flow measurements have been conducted on the ear installed in a 3D-printed model head. The student involved will
1) Analyze the velocity field data already acquired
2) Develop designs for controlling the flow in the vicinity of the ear to reduce noise.
3) Acquire additional acoustic and flow measurements with the flow control devices applied will be conducted to characterize the effectiveness and change in the acoustic source field.
HBK 4620 Acoustic Transducer with Pinnae and Ear Canal
The Gas Dynamics and Propulsion Laboratory (GDPL) is located on campus, at a satellite research park, and in the Medical Sciences Building, and affords the researcher exceptional experimental and computational facilities. The laboratory occupies a high bay area with over 10,000 square feet of floor space. The most advanced flow and propulsion diagnostics are available, in addition to state-of-the-art computational capabilities. A brief description of the research topics performed at GDPL follows.
The advent of jet engine as a power plant for military and civil aircraft and its unavoidable counterpart, jet engine noise, initiated substantial research on the sources and causes of jet noise, as well as methods and devices for its reduction. The noise level of jet engines, particularly during takeoff and climb, is often a concern for people living near airports or working near airplanes. Such high noise levels can limit future airport air traffic expansion, and force new airports to occupy remote sites. It also limits the ability of personnel to work for extended times near airplanes. New requirements for lower jet noise are a continued area of interest both by governmental agencies and by neighborhoods located in close proximity to airports, flight paths and to engine and flight vehicle manufacturers. Due to these concerns a need to further jet noise reduction technology is in demand.
Various approaches have been proposed to overcome the noise issue. The optimal solution should be such that substantial noise suppression is achieved using a method that is easy to implement, low cost, reliable, and without substantial adverse effects on the engine performance. Development of such devise requires basic understanding of the noise generation mechanisms. The objectives of our research are to evaluate experimentally new concepts for jet noise reduction and to develop analytical or numerical tools for the prediction of jet noise and jet noise reduction techniques for commercial and military engines (subsonic and supersonic jets).
Considerable amount of work in the area of passive and active combustion control for gaseous and liquid fueled combustion has been reported during the last two decades. These studies have dealt mostly with bluff-body-stabilized combustor and dump combustors where the recirculation induced by a bluff-body or by a sudden expansion is used to stabilize the flame and were more recently extended to swirl stabilized combustors. Active control strategies have been used to suppress thermo-acoustic instabilities resulting from a coupling between the heat release and the acoustic modes in the combustor. These control strategies have generally relied on modulating the fuel injection and phase shifting it so as to decouple the pressure rise and heat release with respect to each other. Control strategies have also looked at improving fuel efficiency and reducing pollutants, and in extending flammability limits. Our research deals with the control of gas-turbine gaseous and liquid fuel combustors with swirlers, bluff body stabilizers and distributed fuel injection for rapid mixing and stabilization. It focuses on investigating the mixing patterns and flame structure in these combustors and developing control strategies for improved performance of gas-turbine combustors.
In addition, we are developing new technology of combustion, called “Flameless Combustion” for gas turbine engines. This technology provides low emissions and very stable combustion and has the potential of becoming the next generation of combustion systems for propulsion and power generation gas turbines.
A pulse detonation engine (PDE) offers few moving parts, high efficiency, high thrust, low weight, low cost, and ease of scaling. These make the PDE an attractive alternative to jet turbine engines for small disposable engines. The near constant volume heat addition process, along with the lack of a compression cycle, lend to the high efficiency and specific impulse, simplicity, and low-cost of pulse detonation engines. Pulse detonation engines have the potential for operation at speeds ranging from static to hypersonic, with competitive efficiencies, enabling supersonic operation beyond conventional gas turbine engine technology. Currently, no single cycle engine exists which has such a broad range of operability. Computational and experimental program is conducted at UC to investigate the performance of an air breathing pulse detonation engine (PDE). This research effort involves investigating such critical issues as: detonation initiation and propagation; valving, timing and control; instrumentation and diagnostics; purging, heat transfer, and repetition rate; noise and multi-tube effects; detonation and deflagration to detonation transition modeling; and performance prediction and analysis. Our lab has a unique hybrid engine that includes an array of 6 PDEs integrated with an axial turbine. This system potentially can replace the entire high pressure core of a jet engine, including high pressure compressor and turbine and the combustor.
A new and unique facility that simulates the flow conditions in an afterburner configuration is operating in our laboratory. The facility includes a combustor with an exhaust duct where innovative strategies of secondary fuel injection can be tested. It is also instrumented for advanced flow and combustion diagnostics. The facility is used to study secondary combustion dynamics in an augmentor configuration. The research emphasizes new concepts for flame stabilization, and investigation of combustion instabilities in augmentors and their prevention using passive control and acoustic liners. The research combines experimental and computational work.
Lift force on modern shaped wings at a high angle of attack relies on complex set of vortices that are formed at the leading edges, flaps, and tips of the wing. At high angle of attack these vortices loose gradually their coherence due to intrinsic flow instabilities. At these conditions, the lift produced by the vortices is reduced and the aerodynamic moments derivatives change from stable to unstable conditions causing loss of controllability and stall. Tests showed that small continuous, pulsating, or flapping microjets that are injected into the separated regions from certain locations on the wing surface could control the behavior of the flow over the wing. Depending on the orientation of the injected microjets, the flow pattern over the wing can be altered to achieve the desired controllability. The microjets injection can therefore be used for flight control without the conventional control surfaces. Controlled actuation of different combinations of microjets based on feedback from sensors distributed over the wing surface can yield the desired pitch, yaw, and roll moments. Moreover, this method incurs little or no drag penalty.
The control system relies on rational activation of pulsating jets. Static and dynamic modeling of the flow topology, aerodynamic responses and actuator characteristics are required for closed-loop control system design. Advanced external flow control and aircraft attitude control architectures and algorithms are needed to cope with the highly coupled, time-varying, uncertain and complex nonlinear aerodynamics that are dynamically and structurally unstable.
The present concept is applicable to attitude control of tailless fighters, reentry vehicles and UAVs, especially micro-UAVs, without requiring control surfaces such as ailerons, rudder, elevator, or flaps. This type of controlled lift can also be used to enhance performance of lifting bodies. The advantage of such a system lies in its aerodynamic simplicity, reduced radar cross-section and ease of miniaturization.
Mechanisms of voice production are not well understood. They involve interaction between flow and structural vibrations of the vocal folds within the larynx; this is the aeroelastic aspect of the mechanism. The interaction between the flow and vibrating folds modify the flow and produces highly vortical flow pattern. This flow includes organizes vortices and random turbulence generates sound via mechanisms described by aeroacoustic theory. The sound is amplified and filtered in the mouth cavity before exiting as voice. Our jet noise research described in section 1 above has many similarities to voice generation mechanisms. Our research investigates the relationship between the flow field and the noise produced by the jet and both experimental and computational tools are useful for the larynx applications. The voice research is a collaborative effort between our laboratory and the Otolaryngology Department at the UC School of Medicine. Our goal is to develop the physical understanding of voice production that will help in developing new medical treatment and surgical procedures for patients with voice pathologies.
In addition to voice research we are collaborating with the Pulmonary and ENT Departments of CCHMC (Cincinnati Children’s Hospital) in applying CFD to compute airway flow and pressure distribution for sleep apnea and airway reconstruction research.
Scramjet combustors are characterized by an extremely short residence time for the completion of fuel atomization, mixing and combustion. It is therefore desired to develop fuel injection schemes that will accelerate the mixing process by improving penetration, achieving small-dispersed fuel droplets, and enhancing mixing. In addition, during vehicle acceleration the location of heat release in the combustor has to shift to ensure optimal performance in the entire range of Mach numbers. This project addresses the aforementioned issues by investigating fuel injection flow control strategies. Specially designed injectors are designed and tested in quiescent, cold cross flow, and reacting conditions. The effect of fuel temperature, as the fuel is heat soaked for combustor cooling, would also be simulated to test the stability of the injectors. Emissions, which are a critical concern for commercial space applications, would also be used as a performance parameter in evaluating the injectors. In parallel with these experiments, numerical modeling is pursued to study the flow physics and effectiveness of the different injector configurations in cold and reacting flows.
Glioblastoma multiforme (GBM) is the most common primary brain cancer and of the most lethal with almost certain patient death within two years of diagnosis1. These tumors can escape the natural host immune surveillance and subvert the physiological role of multiple brain cell types including vascular endothelial cells of the blood-brain barrier (BBB) and immune cells2,3. Standard therapy for GBM consists of surgical resection of the main tumoral mass followed by radiation and chemotherapy4. Except for a few exceptions, tumors initially respond to these treatments, however, no current regimen can overcome tumor recurrence after which the chances of patient survival drop drastically to 6 months. While the exact mechanisms underpinning drug resistance are still largely unclear, the current leading hypothesis is that a small percentage of cancer cells with self-renewal potential, also named glioblastoma stem cells (GSC)5, could survive and be selected during the therapy. Such a limited population of resistant GSCs may eventually spread undetected through the brain and regenerate the tumoral mass during recurrences. Targeting GSCs and their specific niches represents a promising strategy for curing GBM, however, the field lacks robust translational models able to capture the complex set of molecular and biomechanical cues that are thought to support GSCs and that are normally generated by the healthy cells of the brain.
In our lab, we have recently established an enabling 3D model of GBM designed to recapitulate peculiar aspects of the brain tumor microenvironment that are known to modulate cancer resistance in vivo and include tissue-specific components of the extracellular matrix as well as human brain cells. This project will consist in conducting a proof-of-concept study to assess drug resistance of patient-derived tumors against existing and novel therapies. We will test the hypothesis that our new in vitro system supports patient-derived GSCs’ survival and maintenance of self-renewal markers when cancer cells are exposed to therapeutics used in the clinic. The project will include training in the use of advanced bioprinting methods, cell culture, and microscopy imaging.
References.
1. Lin, D. et al. Trends in Intracranial Glioma Incidence and Mortality in the United States, 1975-2018. Front. Oncol. 11, 748061 (2021).
2. Pacioni, S. et al. Brain Invasion along Perivascular Spaces by Glioma Cells: Relationship with Blood–Brain Barrier. Cancers 12, 18 (2019).
3. Himes, B. T. et al. Immunosuppression in Glioblastoma: Current Understanding and Therapeutic Implications. Front. Oncol. 11, 770561 (2021).
4. Stupp, R. et al. Effects of radiotherapy with concomitant and adjuvant temozolomide versus radiotherapy alone on survival in glioblastoma in a randomised phase III study: 5-year analysis of the EORTC-NCIC trial. Lancet Oncol. 10, 459–466 (2009).
5. Gilbertson, R. J. & Rich, J. N. Making a tumour’s bed: glioblastoma stem cells and the vascular niche. Nat. Rev. Cancer 7, 733–736 (2007).
6. Dogan, E. et al. Cancer Stem Cells in Tumor Modeling: Challenges and Future Directions. Adv. NanoBiomed Res. 1, 2100017 (2021).
Large-scale injuries to bone tissue can have many causes, including traumatic injury, birth defects, or as a side effect for cancer treatment. In particular, bone defects greater than 2cm in length are termed “critically-sized” since they often cannot heal spontaneously. These large bone injuries are often treated with autologous bone grafts, or bone tissue harvested from the patient’s own body, though these procedures are limited by donor site morbidity and a limited amount of harvestable bone. To overcome these shortcomings seen with bone grafts, our lab is seeking to develop synthetic, “off-the-shelf” systems to regenerate these large bone injuries. We are currently developing an injectable drug delivery system made from coated microparticles that can release multiple therapies in sequence to promote the growth of new blood vessels and new bone tissue. The ~10µm particles, made from the polymer poly(propylene sulfide) (PPS), can be loaded with bone-regenerating drugs during fabrication but are small enough to be injected from a syringe. These particles can also be coated with a separate vessel-regenerating drug (Figure 1A). Importantly, both the drug coating and drug-loaded particles are selectively degraded by cell-generated reactive oxygen species (ROS). This allows for sequential drug release from the injected microparticles after triggering by the local cells at the bone injury site (Figure 1B-D).
For this proposed project, the Protégé Scholar will be heavily involved in the development of these coated microparticles. The Protégé Scholar will assist in optimizing the particle coating process, measuring drug release kinetics, and evaluating the biological response of this system in preparation for future pre-clinical testing in more complex biological models
Figure 1. Overview of the dual therapy system. a) Synthesis of drug loaded PPS microparticles coated with drug loaded LbL thin films. b) Injection of the system into a critically-sized bone defect. c) Initial ROS-degradation of thin film and pro-angiogenic drug release, followed by d) ROS-degradation of PPS microspheres and pro-osteogenic drug release.
Dr. Hoilett is an Assistant Professor of Biomedical Engineering. He graduated from Purdue University in 2021 with a PhD in Biomedical Engineering and from Vanderbilt University in 2014 with a Bachelor of Engineering also in Biomedical Engineering. His academic interests involve developing wearable sensors for mobile health platforms and engaging engineering design activities for undergraduate and graduate students. He has several years of experience with analog circuit design and embedded systems. His previous work includes developing a wearable opioid overdose monitor for substance use disorder patients and developing an impedance analyzer for a microfluidic blood-brain barrier model among other projects. On the education side, he has developed several lab activities for first year and junior level Biomedical Engineering students. He was instrumental in developing the Milestones Program at Purdue, a certificate-granting series of workshops providing students professional engineering skills utilized in rapid-prototyping and industrial applications. At the University of Cincinnati, Dr. Hoilett’s lab will continue developing low-cost diagnostics and sensors for improving patient-care both in high-resource and low-resource settings, tackling healthcare disparities and unmet clinical needs worldwide.
Babies born premature (approximately 10% of the population), can experience a range of neurological, ocular, respiratory, gastrointestinal and musculoskeletal impairments. For these infants, proper nutrition in the early stages of life is crucial to achieving short-term clinical milestones and long-term growth and development. The best nutrition source for premature newborns to achieve these goals is breastmilk but preserving the nutrient benefits of this complex liquid biologic tissue can be very challenging.
It has been established that there is substantial adsorption of macronutrients to the surfaces of containers, feeding tube lines, and other interfaces, a process that often reduces the total nutrient delivery to the infant. For donor milk, the nutritional loss is especially severe because there are a considerable number of steps between expression of the breast milk and its delivery to the infant. These include, pasteurizing, screening, pooling, freezing, transporting, thawing, preparing, and administering the milk. Each step offers the potential for macronutrient loss, and it is particularly detrimental to infants that require tube feeding. In order to improve clinical outcomes for at-risk infants, it is critical to ameliorate this macronutrient loss.
While others have examined single components of the milk transfer system, we propose to apply a systems-level analysis to the entire milk transfer system and identify the points where macronutrient loss is the greatest. We will then use a patented technology to develop a polymer-based lining material that will prevent macronutrient adsorption and significantly improve nutrient delivery to infants, especially those in the NICU. This project’s specific aims are:
Aim 1: Characterize the amount of macronutrient loss through current collection, storage, and handling methods utilized in the processing of freshly expressed and frozen (mother’s and pasteurized donor human milk (PDHM)) and determine critical points of loss within the system.
Aim 2: Demonstrate the ability of pharmaceutical grade polyethylene glycol (PEG), a strongly hydrophilic molecule, and calfactant (trade name Infasurf), a naturally derived surfactant, to significantly decrease nutrient loss from polymers in the milk handling system.
Aim 3: Demonstrate the successful translation of nutrient-protecting coatings in a prototype milk-transfer system.
This project is in collaboration with Cincinnati Children’s and Professor Eric Nauman’s Human Injury Research and Regenerative Technologies (HIRRT) lab.
Figure 1 – Process to quantify macronutrient loss using 3 mL aliquots. The Miris HMA, will be used to obtain baseline values for lipids, proteins, carbohydrates, and total energy. Differences between stages of the milk transfer process will be quantified and used to determine the most important elements of the system to modify.
Pressure ulcers (PrUs), also known as bed sores, occur when the skin is exposed to pressure for a long period of time. This constant pressure results in decreased perfusion (blood flow) through a localized area of skin. Decrease in perfusion results in injury to the tissue with varying depth and severity. Current guidelines set by the National Pressure Ulcer Advisory Panel (NPUAP) are based solely on observation of the tissue, the wound bed of the PrU, and feeling the affected area for temperature or elasticity changes. Categorization is according to the guidelines (Braden Scale), as shown in Figure 1. This approach is an immense source of error in PrU diagnosis as it is subjective and vague. For example, the NPUAP guidelines state that a Stage 1 PrU (Fig. 1A) may be “painful, firm, soft, warmer or cooler as compared to adjacent tissue”. PrUs have significant patient morbidity and high costs to healthcare facilities. Early detection of erythema can prevent the progression of ulcers at stage I or II to more serious Stage III or Stage IV pressure ulcers.
Total Contact, Inc. is developing the CPI that, in rapid succession, acquires three-dimensional surface, color, thermal, and perfusion images of a localized area on the skin (Fig. 1B). This study will determine if the CPI can capture consistent, quantifiable images of potential and existing PrUs and, when staging pressure ulcers using the CPI vs. current subjective methods, if algorithmic analysis of the image data correlates with current subjective assessment methods.
The student will work with a senior member of Total Contact, Inc. to assist in combining the imaging modalities for an integrated system to be used bedside. Imaging of PrUs will be conducted at Miami Valley Hospital alongside clinicians as they conduct the hospital’s subjective protocol.
The student may be involved in data collection and determine if the CPI can consistently capture quantifiable images of potential and existing PrUs. The student will participate in the application of the image data, extracting parameters of interest such as surface area and color measures, to assess whether algorithmic analysis of CPI image data correlates with the subjective assessment methods currently used.
This project is in collaboration with Total Contact, Inc. and Wright State University.
Angelman syndrome (AS) is a neurogenetic syndrome associated with severe developmental and intellectual disability. Symptoms of AS include very limited speech, difficulty sleeping, and poor motor function. AS is caused by a mutation or deletion of the UBE3A gene on the maternal chromosome 15 and is typically diagnosed in the early childhood period using genetic testing. At present, there is no cure for AS. Treatment is focused on supportive therapies and pharmaceuticals to manage seizures and reduce behavior problems. The AS community is motivated to find a cure, and several major gene therapy trials are underway to reduce or potentially reverse symptoms.
Despite increased investment in clinical trials, functional outcomes that impact the lives of people living with AS and their families remain widely variable. A major barrier to clinical trials is the lack of available outcome measures suitable for AS. Wearable devices that monitor physiological and behavioral output are promising solutions because they provide objective metrics of physiological function without requiring verbal or motoric input from the patient. However, typical wearable devices in form factors such as smartwatches and headbands are often not tolerable by AS patients. Using input from AS caregivers from extensive focus groups (N = 8) conducted by our research team, we have designed MyA, a biometric vest that will measure several key signals relevant to AS (heart rate, respiration, vocalizations, temperature, and sleep), while meeting the unique sensory and tactile needs of the AS population. For our preliminary developments, we sewed conductive fabric and conductive silicone into separate commercially available athletic vests composed of primarily nylon, polyester, or polyamide. Our preliminary measurements of the electrocardiogram demonstrate the ability to capture key biosignals using our textile prototype. We were able to measure heart rate from the electrocardiogram within 2.4 beats per minute of a commercially available reference chest strap heart rate monitor with high correlation between the two devices (r = 0.88, p < 0.05).
For the proposed project, the student researcher will work closely with a senior member of the lab to integrate audio and video capabilities into the vest. Audio and video are important behavioral inputs that allow us to understand levels and styles of communication in people with AS. We would also like to understand how people with AS interact with others and their environment, and vice versa. The student will work with the senior member of the lab to validate each sensor on the benchtop and develop code that can be integrated seamlessly into the biosensor prototype.
This project is in collaboration with Purdue University Department of Psychological Sciences.
Figure 1. MyA system block diagram depicting essential internal functions as well as connections to the textile.
Worldwide, premature birth accounts for 30% of all neonatal deaths in children under the age of five. Neonatal hypothermia is one of the most common complications of premature birth as newborns are unable to regulate their body temperature. Hypothermia is an especially devastating complication of premature birth in low-resource settings. Over 80% of deaths due to premature birth occur in low and middle-income countries (LMICs), due to a lack of access to incubators that are critical for managing hypothermia. Furthermore, LMICs lack the necessary tools to regularly monitor the baby’s vital signs, which is critical for managing complications due to premature birth. Deaths from sudden infant death syndrome (SIDS) and accidental suffocation are silent and go unnoticed without continuous vital sign monitoring.
Kangaroo mother care (KMC) is a proven intervention for combating neonatal hypothermia and involves skin-to-skin contact between the caregiver and the newborn. However, KMC places high demand on caregivers, and leaves newborns with no protection when caregivers require a break to care for themselves. Furthermore, it is very difficult to measure a baby’s vitals during KMC as the baby is swaddled tightly to the caregiver and is not accessible. As a result, KMC still leads to deaths due to SIDS or accidental suffocation as the caregiver is unaware of the baby’s vitals during KMC.
While some low-cost warming devices exist, such as the Embrace Infant Warmer, Warmilu), and the Dream Warmer, these warmers are either not compatible with KMC or are not able to monitor vital signs.
Hypothesis: Therefore, a low-cost warmer that is compatible with KMC, can provide thermoregulation during breaks in KMC, and can measure key vital signs to prevent SIDS and accidental suffocation would revolutionize neonatal care in the hardest hit global settings.
Our patented device, NeoWarm, is a disinfection wipe-friendly infant carrier that serves the need for thermal management and vital signs monitoring of premature infants during and in between KMC. NeoWarm has integrated fabric heating pads that generate heat from a lightweight, rechargeable, portable battery pack in similar fashion to an electric jacket. NeoWarm also includes sensors for heart rate, respiratory rate, blood oxygen, and temperature, to monitor the infant’s key vital signs to detect signs of hypothermia and other complications such as apnea or SIDS. NeoWarm is safe and effective as demonstrated in pilot studies using hypothermic newborn piglets. NeoWarm was able to warm hypothermic pigs to normal, core body temperature, while piglets struggled to reach normal body temperature without NeoWarm. Given the strength of our benchtop and preclinical studies, our present study aims to validate NeoWarm in a clinical setting with human babies in collaboration with the Indiana School of Medicine and Moi University College of Health Sciences in Eldoret, Kenya.
Figure 1. A) Water temperature rises from mild hypothermia (35oC) and plateaus at normal body temperature (37oC) (n = 3, error bars represent standard deviation). B) HR from PPG and ECG show significant correlation with reference (r = 0.60 and 0.69, respectively, p ≤ 0.01) C) Measured breaths per minute is within 1 breath of reference D) Relative blood oxygen measurements show similar decrease in percent saturation (7%) during breath hold (gray region) compared to reference (9%).
During transport, newborns experience quite a bit of physical forces due to the different vehicles and mediums involved in the transport process. The effect of the cumulative forces applied to the newborn may have deleterious effects on their development; however, this phenomenon is not well-studied or characterized. Therefore, we’re developing a miniaturized device that can be placed at various locations around an ambulance, helicopter, airplane (and other transport vehicles) and around the transport incubator to measure the forces applied to the newborn during transport.
This project is in collaboration with the neonatal intensive care unit and transport teams at Cincinnati Children’s and Cincinnati Medical.
Figure 1. An early prototype of Peapod, a device with integrated motion and audio sensors for measuring forces experienced by a newborn during transport.
A wide variety of medical applications utilize electrochemical biosensors, notably glucose monitors for patients with diabetes. As wearable electronic devices for health monitoring applications have become increasingly popular, there is a push for these biosensor devices to measure analytes in the user’s sweat, becoming smaller, faster, and easier to interface with. These biosensors depend on potentiostats, instruments capable of measuring electrochemical cells necessary for amperometric sensing. We have previously developed KickStat <https://www.mdpi.com/1424-8220/20/8/2407>, a miniature potentiostat that can measure cocaine in simulated sweat using cyclic voltammetry and square wave voltammetry. KickStat can also perform general electrochemical measurements of potassium ferricyanide using chronoamperometry and normal pulse voltammetry. We are improving our hardware to include Bluetooth Low Energy (BLE) capabilities, allowing KickStat to wirelessly interface with a smartphone to send data and configure system settings. KickStat will also include software adjustable gain and multiple channels for simultaneously measuring multiple analytes while maintaining the continuous demand for smaller hardware.
To make it easier interfacing with KickStat easier, we are developing a graphical user interface (GUI), allowing researchers and students to easily to interface with KickStat. The GUI will allow users to send necessary commands to send necessary commands, and receive data all within an easy to user, plot and analyze the data to interpret the signals that were received. and easy to read interface.
Figure 1. KickStat, a miniaturized potentiostat for measuring electrochemical signals. Image reproduced from: O. S. Hoilett, J. F. Walker, B. M. Balash, N. J. Jaras, S. Boppana and J. C. Linnes, Sensors, 2020, 20, 2407.
The Protégé student will be paired with a Ph.D. student and assist in the research and development of continuous electrochemical aptamer biosensors for chronic disease monitoring. Current focus is on developing sensors related to heart failure, insulin for diabetes patients, and cortisol for stress monitoring. The sensors are adapted to work with existing continuous glucose monitor wearables (also known as ‘CGM’). The work involves basic wet-chemistry, device fabrication, electronic testing, and data analysis/presentation. Students begin with gold electrodes, and the place down special DNA-based chemistry (aptamers) that can react with and measure the molecule to be measured, providing an electrical signal that can then be reported on a smart phone to the user. A goal for the Protégé includes co-authorship on at least one publication resulting from the work with the Ph.D. student.
The vascular smooth muscle cells (VSMCs) that comprise the medial layer of arteries exhibit two distinct phenotypes: contractile and synthetic. Contractile VSMCs regulate blood pressure in the artery but can dedifferentiate into the synthetic phenotype in response to injury. We are hypothesizing a potential third phenotype of VSMCs initiated by mechanical strain caused by hypertension, known as the silent killer. We propose that this third phenotype happens through the Wnt signaling pathway as VSMCs become osteoblast-like cells and deposit mineral into the arterial extra cellular matrix. This project would provide new knowledge by confirming the continued plasticity of VSMCs caused by mechanical strain activating the canonical Wnt signaling pathway. By understanding the signaling pathway associated with this phenotypic modulation of VSMCs, we could work to develop targeted therapeutics to treat vascular calcification at the cellular and molecular level.
My research group has optimized and validated an in vitro model approach for inducing phenotypic modulation and calcification, we studied the calcium content in primary aortic smooth muscle cells. Inorganic sodium phosphate was used because it is known to induce phenotypic modulation and calcification in vascular smooth muscle cells. The calcium content for the phosphate-treated groups was significantly increased compared to the control groups. To further confirm the model’s ability to induce phenotypic modulation and calcification, we performed scanning electron microscopy (SEM) and energy-dispersive x-ray spectroscopy (EDS) to visualize and quantify the calcification present in the samples [Figure 1]. Given our ability to induce phenotypic modulation through phosphate supplemented media and literature hypothesizing this phenotypic switch occurs through the canonical Wnt signaling pathway, we want to examine this pathway as a therapeutic target. This protégé project would involve confirming the role of Wnt signaling in synthetic vascular Smooth muscle cells.
Experimental Plan:
1) Induce smooth muscle cells into a synthetic phenotype.
2) Examine the stability of the synthetic phenotype.
3) Confirm Wnt signaling as essential for phenotypic modulation.
Training provided:
- Polymer synthesis
- Materials characterization
- Aseptic technique
- Cell culture
- Potential for research publications and presentations at local and national conferences
Figure 1. The addition of inorganic phosphate significantly induced phenotypic modulation and calcification as compared to controls in calcified cells over 7 and 14 days (p<0.05). SEM images demonstrate the increase in mineral nodule formation in (Fig 1C & 1D) calcified cells over controls (Fig 1A & 1B). EDS analysis confirmed the presence of calcium and phosphorus ions in the mineral nodules. Figure 1C: 10.95% Calcium by weight. Figure 1D: 22.63% calcium and 16.02% phosphorus by weight.
Figure 1: (A,B) Scanning electron microscopy image of electrospun PVDF polymer of defined chemical, physical, and electrical properties with Schwann cells growing on fibers. Confocal microscopy showing (C) Schwann cells in a 3D z-stack projection on PVDF and a (D) maximum intensity image showing alignment of cells on fibers.
Peripheral nerve injuries impact millions of Americans each year with many more living with the effects of traumatic nerve injuries. In severe peripheral nerve injuries, nerve pathways, connections, and the extracellular matrix (ECM) tissue surrounding nerve that lead to the sensory or motor targets are damaged. If the injury gap is larger than 2 centimeters, functional recovery is extremely limited and no adequate therapies are currently available. This deeply impacts the quality of life due to the loss of connection between the central nervous system and the body’s extremities. Neurons do not have the ability or needed signals from the damaged ECM surrounding the injury site to allow guided growth of axons across the injury space in order to regain function. Therefore, this project will address the urgent need to engineer novel biomaterials that give the proper electrical, physical, and chemical signaling to cells and neurons for guided nerve regeneration and provide functional recoveries in traumatic nerve injuries. This will be accomplished by engineering biomaterials (Figure 1A,B) to possess the proper physical, electrical, and chemical signals in order to direct cell alignment and growth. We will develop these biomaterials to deliver defined, tunable signals to the cells in order to elicit the desired cellular outcomes (Figure 1C,D). It is hypothesized that the biomaterial, in combination with relevant cells and ECM, will functionally bridge the injury gap to restore function to injured tissues.
Current efforts in the area of ocular or intra-articular drug delivery include frequent direct injections, which is not only invasive and inconvenient for patients but also may increase the risk of complications. Therefore, development of stable drug delivery systems which have ability to be released in a controlled manner for the long term is necessary.
This research project is about developing dose-controllable implants, which release drug on-demand, and determining drug release kinetics. Drug inside the implant capsule made of biodegradable polymer is released upon exposure to light. During the summer, you will have experience on developing polymer capsules and examining characteristics of drug delivery.
The advisor will provide basic principles in soft materials, drug delivery, and various analytical technique.
Basic chemistry lab experience is required.
Figures A, B, and C: Implant that releases drug through nanopores.
Fig. 1: Contrasting a. traditional PCR-based molecular diagnostic workflow with the proposed b. novel heating mechanism. A rotating disc with embedded conductors surrounded by magnets induces eddy currents that can raise temperature of fluidic samples. The spinning platform can also leverage centrifuge-based sample preparation workflows to enable pre-PCR nucleic acid extraction. Integrating a smartphone-based fluorescence detection of post PCR analysis enables inexpensive and portable “sample-to-answer” molecular diagnostic platform.
Problem statement: The recent global pandemic (COVID-19) has exposed some of the key limitations in our current infectious disease management systems, particularly when applied in remote underdeveloped areas. Existing approaches (like the Polymerase Chain Reaction (PCR) tests) are highly resource-intensive, relying on people depositing their biological samples to collections centers where trained personnel process these samples in dedicated laboratories for further analysis. These inefficient channels introduce a considerable time lag between sample collection, diagnosis, and implementation of countermeasures. A need, therefore, exists for developing inexpensive and simple tools that can be broadly deployed to accelerate diagnosis, and provide real-time data to better inform decision making.
Project Description: The Protégé student will work in Dr. Priye’s laboratory to develop inexpensive and simplified instruments/protocols that can replace traditional bulky, expensive and power intensive laboratory instruments required for infectious disease diagnostics. One of the major challenges associated with making PCR tests more accessible is the need for thermal cyclers which repeatedly heat and cool the biological samples using power consuming Peltier heating elements. We will explore unconventional and novel techniques of heating samples that are more efficient and inexpensive such as heat generation via eddy currents and lasers. Detection of PCR tests is accomplished using expensive fluorometers. We will explore simpler optical setups such as the use of smartphone cameras or raspberry pi cameras to read fluorescent signals from PCR tests.
Learning outcomes: Along with gaining research experience in the laboratory, the protégé student will learn and apply 3D printing, CNC machining, Arduino and python programming, Microfluidics technology and physics-based modeling. Students are encouraged to document their results and successful completion of the project can result in a journal publication.
Developing sustainable aviation fuel (SAF)from waste biomass has great potential to reduce U.S. dependence on fossil fuel while improving national energy security and addressing the environmental issues. The Renewable Fuel Standard mandates 36 billion gallons of biofuels should be produced annually by 2022, with 16 billion gallons coming from lignocellulosic biomass. Although ethanol has been the main candidate of transportation biofuels, butanol can be easily upgraded into SAF. SAF is one of the promising advanced biofuels being pursued by the Department of Energy (DOE) and National Science foundation (NSF) for the next generation of alternative fuels. However, one of the major bottlenecks impeding production of SAF from renewable biomass is the lack of cost-effective processes for converting biomass into biofuels including butanol.
Biomass pretreatment is needed to break down the recalcitrant structure of the biomass cell wall for subsequent enzymatic hydrolysis and fermentation. However, the pretreatment processes generate inhibitors from the degradation of cellulose, hemicellulose and lignin, many of which significantly reduce the microbial growth and fermentation productivity during the fermentation process. Detoxification methods are required to reduce the toxicity of hydrolysates for biofuels fermentation, but they increase the total production cost significantly. We hypothesize that nucleophiles can react with carbonyl inhibitors in biomass pretreatment process and enhance butanol production. To verify this hypothesis, we will design new detoxification processes with the addition of nucleophilic amino acids and proteins for in situ removing the inhibitors in hydrolysates and optimizing the microbial fermentation in bioconversion processes. The protégé students will work on process design with hands-on experience in process design and microbial fermentation.
Neuromorphic Computing and Artificial Intelligence: Artificial Intelligence (AI) has caught significant research attention. However, AI algorithms are compute resource intensive. Therefore, much emphasis has been devoted on developing specialized neuromorphic System on Chip (SoC) for accelerating AI recently. Some examples of these neuromorphic-SoC include Google’s TPU, Intel’s Nirvana and Loihi, and IBM’s TrueNorth. In spite of these significant advances, the performance of these processors are limited by the lack of novel reconfigurable memory devices that can mimic the adaptive characteristics of biological synapses. MIND lab researchers have invented new type of artificial synaptic devices, referred to as, Low-Energy Evolutionary Channel Electronic Synapses (LEECHES) that can provide lucrative options for neuromorphic SoC. The student working on this project will work on this cutting-edge technology and develop neuromorphic SoC utilizing these novel memory devices. The student will perform the following tasks:
o Testing and Modeling of LEECHES in Verilog/VHDL Biological computing elements are mimicked by developing novel nanoelectronic artificial neurons and synapses and assembled in brain-inspired cortical circuitries and architectures to create artificial brains and neuromorphic
o Modeling and simulation of neural circuit modules around LEECHES
o Implementation of learning algorithms and performance evaluation of this novel neuromorphic SoC
o Publication and presentations.
o Training data collection on drones fitted with cameras and multiple sensors.
Biological computing elements are mimicked by developing novel nanoelectronic artificial neurons and synapses and assembled in brain-inspired cortical circuitries and architectures to create artificial brains and neuromorphic processors.
Trusted and Secured Microelectronics Hardware: Due to complex supply-chain of microelectronics integrated circuits (IC) design and fabrication, hardware security has emerged out to be one of the prime concerns. This project seeks to develop novel ways to design and fabricate secure microelectronics circuits using emerging nanoelectronics logic and memory devices. The students will be involved in the design of ICs, simulations, fabrication, and testing. A fundamental question we will try to answer is how can design itself be made more trust-worthy and resilient? Can emerging nanoelectronic memory and logic devices offer any inherent benefit in this area?
By identifying unique characteristics of nanoelectronic emerging logic and memory devices we can design Integrated Circuits are inherently more secure against hardware attacks.
Advanced Semiconductor Logic and Memory Devices: With the end of Moore’s Law of conventional transistors scaling, novel logic and memory components are needed to address the demands of the next generation of computing. This project will train students on fabrication and testing of next generation of logic and memory devices. DNA based computing and data storage approaches will also be explored.
Dr. Rashmi Jha, who is the director of MIND lab, has more that 15 years of experience in the areas of nanoelectronic logic and memory devices, neuromorphic devices, circuits and architecture, and microelectronics in industry (IBM Research) and academia. MIND lab provides an excellent research environment to the students and is currently supporting 5 PhD, 5 MS, 4 UG students. The students will work in the team of graduate, and undergraduate students, and PI in these stimulating research areas. Students will be mentored via weekly group meeting and one-to-one interactions with PI and encourage to publish work and attend conference.
The next release problem (NRP) is rooted in the practical challenge of determining which subset of the candidate features should be added to the software system as part of the next release, and which other features would not be delivered in the upcoming version. Solving the NRP is critical for balancing diverse stakeholders’ evolving needs and software implementation’s resource constraints. For example, among the ten Zoom features listed below, if only five features could be released in the next version, which five should Zoom work on? This example illustrates the NRP, and software projects adopting agile development processes face the challenges associated with the NRP on a continuous basis. This Protégé research project is aimed at leveraging machine learning algorithms to solve the NRP. The Protégé student will: (1) studying relevant literature on machine learning, NRP, and natural language processing (NLP), (2) developing algorithms to process the textual requirements data and learn to solve the NRP, and (3) experimentally evaluating the algorithms’ performances.
Can you help Zoom to decide which five features to release next, and which features to be postponed beyond the next version? The Protégé project is aimed at exploiting machine learning techniques to solve this kind of problems with real-world data from the software industry.
Topic 1: 3D Microfluidic Devices for Neural Studies: A neural circuit is a group of neurons interconnected to each other to perform certain function, while interconnected neural circuits form larger brain/neural networks. The study of neural circuits is important to help understand brain functions and the causes of neurological disorders such as autism spectrum disorder and schizophrenia. Traditionally, neural circuit characterizations are done by in vivo magnetic resonance imaging (MRI), which typically can only identify the circuit locations in the brain.
Blood-brain barrier (BBB) refers to the biochemical, metabolic and protective interface between the brain and the capillary blood vessels within it. It prevents irregular changes in the environment like neurotoxic components from reaching the brain but allows nutrition and oxygen to go through to support the brain. Study of BBB is of great interest to scientists and clinicians as the integrity of BBB is essential for the functionality and health of the brain. BBB dysfunctions are implicated in a collection of neurological disorders, e.g., Alzheimer’s disease. In vitro reconstruction of BBB is of high interest but has been challenging at least partially due to the difficulty in reproducing the circulation environment required for BBB to form at a size scale that suits organoids.
Microfluidic devices with separate compartments and interconnecting channels have been used to culture neurons and study the neural circuitry. Similar devices have also been formed to culture blood vessel cells under continuous flows. However, these existing devices are typically made in a planar 2D configuration that is suitable for cells but with limited capabilities or necesary 3D features to address the needs for larger brain tissues and organoids.
This summer project will allow the Protege students to participate in the work on the development of the 3D neural study devices with graduate students and be exposed to interdisciplinary research in the field of MEMS and microfluidics, collaborating with Cincinnati Children’s Hospital Medical Center and contributing to research tasks including literature review, design, 3D printing, hands-on microfabrication using the cleanroom facility, and testing in vitro of the fabricated devices. Multiple students can be accommodated.
Fig: (a) Concept figure showing exploded view of the 3D microfluidic device for culturing blood vessel and brain organoids; (b) preliminary results showing blood vessel organoid cultured in the microfluidic device, indicating effective 3D flow generation in the culturing site. GFP (b, green) is a protein that composes the blood vessel cells, and DAPI (c, blue) is a marker that the cells have taken from the fluid that circulated in vertical channels of the device and diffused to the organoid.
Topic 2: Wireless Magnetoelastic Sensors for Biomedical Applications: Magnetoelastic (ME) materials have been universally used as anti-theft security tags in shops. These materials exhibit the magnetostriction behavior in which the magnetic property of the material changes under mechanical deformation (strain). The application of such materials as sensors, particularly implantable microsensors for putting into the human body for biomedical applications, is of high interest due to its inherent passive wireless nature, which eliminates the needs for battery or antenna, leading to implanted devices with reduced complexity, size and cost. The micro electro-discharge machining (µEDM) is a computer-controlled, effective micromachining technique for patterning ME materials for sensor fabrication with the micron-scale feature sizes. This tool is available in house at the MEMS and Autonomous Integrated Microsystem (AIM) Laboratory.
This summer project will allow the Protege students to work on the development of a ME sensor for biomarker detection with graduate students and be exposed to interdisciplinary research in the field of MEMS and microsystems, collaborating with UC School of Medicine and contributing to research tasks including literature review, design and simulation, hands-on microfabrication using the cleanroom facility, and testing in vitro of the fabricated implantable microsensors. Multiple students can be accommodated.
Fig: Illustration showing device concept diagram of wireless biosensor for early detection of periprosthetic joint infection (PJI) in newly implanted knee joint prosthetics, as an example application of magnetoelastic (ME) sensor for implantable biomedical applications.
A side-channel attack can infer the secret key on a device (e.g., a microcontroller, a secure chip on a credit card, or an IoT device) by analyzing power consumption when the device runs encryption algorithms, such as Advanced Standard Encryption (AES). It is one of the primary threats to the security of embedded systems. While countermeasures (e.g., random delays, hiding, and masking) have been proposed to defend against traditional side-channel attacks, recent deep-learning-based side-channel attacks can defeat these existing countermeasures. Despite the promising results reported in recent studies, deep-learning-based side-channel attacks are not robust as they are sensitive to discrepancy between training data and test data. For instance, a deep neural network trained with data collected from one microcontroller (e.g., 8-bit XMEGA) may not derive high accuracy over data collected from another microcontroller (e.g., 8-bit XMEGA) due to minute changes in power measurements.
This project aims to enhance the robustness of deep-learning-based side channel attacks. The students in this project will have the opportunities to (1) Study research papers related to deep-learning-based side-channel attacks; (2) Explore new architectures of neural networks that can be more robust in side-channel attacks; (3) Examine different target devices, including microcontrollers and FPGAs; (3) Learn cybersecurity and machine learning knowledge and skills related to this project; (4) Have access to GPU machines in Dr. Wang’s lab for training neural networks; (5) Have access to data collection platform (Chipwhisperer) and corresponding microcontrollers in Dr. Wang’s lab to collect power and EM (electromagnetic) traces of AES encryption for analysis. This opportunity is open to students in Computer Engineering, Computer Science, or Cybersecurity Engineering.
Data collection setup in Dr. Wang's lab
UAV MASTER Lab and CDS Lab
Unmanned Aerial Vehicles (UAVs) or drones have generated a lot of interest recently among the research community due to their potential to revolutionize some of the applications in civilian domain such as emergency management, law enforcement, infrastructure inspection, precision agriculture, package delivery, and imaging/surveillance. While there has been a lot of progress in drone applications in outdoor environments, indoor usage of drone has been limited even though there are several applications such as warehouse management and indoor emergency response. The objective of this project is to build a drone that can deliver telehealth services to people inside their homes. Operation of drones in indoor environment is particularly challenging due to several reasons including loss of access to GPS information, and proximity with obstacles and humans. For safe operation of UAVs in indoor environment, some level of autonomy is needed to allow UAVs to avoid collisions and carry out basic maneuvers without any assistance from humans. Incorporating autonomy in drones operating in indoor environment is often challenging due to the fact that positional feedback from GPS is intermittent or unavailable. The UAV needs to solve the problem of localization, i.e., finding its position and orientation using onboard sensors such as vision, laser, or other proximity sensor such as ultrasound sensors, via a process called Simultaneous Localization and Mapping (SLAM). Furthermore, the UAV should be able to use its positional estimate to perform navigation in a precise manner to enable safe operation. The objective of this project is to develop hardware and software means to carry out the process of SLAM and autonomous navigation of UAVs in indoor environments. To alleviate the safety issue arising due to operating close to humans, a prototype is being developed that can be remotely controlled via cellular network. This prototype will have inbuilt intelligence for obstacle avoidance, autonomous landing, communication delay, and lost communication. Apart from the hardware and software components, the project would involve carrying out flight tests in indoor and outdoor environments. This is a part of ongoing National Science Foundation funded project that involves researchers from multiple disciplines including College of Nursing and College of Allied Health Sciences. The student will be working in a multidisciplinary team of researchers and graduate students.
The production of metals is responsible for approximately 30% of greenhouse gas emissions, and it is projected that demand for metallic materials will continue to increase until at least the year 2060 to meet demand for renewable energy installations. The Department of Energy is investing billions of dollars to bring green energy innovations to market and create clean energy jobs in the United States. Improving useful life and properties while simultaneously controlling costs is key to reaching sustainable utilization of metallic materials. In this project, the student will contribute to the design and development of alloys for the circular economy, considering end-of-life recyclability and reuse. Students will gain exposure to:
- Synthesis of metallic specimens using vacuum arc melting
- Deformation processing of metals
- Prediction of solidification behavior and microstructure of alloys using commercial software packages
- Operation of microscopes and microstructure characterization techniques
- Mechanical testing of materials
- Scientific methods for alloy development
- Industrial-academic collaborations to solve significant challenges for sustainability
- Conducting a literature review
Microscopic structure of a crack growing in a steel alloy. Different colors come from the different crystals in the material, revealed using electron backscatter diffraction microscopy. The black bar in the lower left is approximately half the diameter of a human hair. Image from V.A. Yardley, S. Fahimi, and E.J. Payton, Materials Science and Technology (2015).
3D Printing, or Additive Manufacturing, has the great potential to revolutionize the industry, and thus make big impact on our economy. 3D printing usually follows a layer-wise building process, until the desired height is achieved. Therefore, products of arbitrary shape can be built without difficulty by using this innovative manufacturing method. One pressing issue with 3D printing is the lack of understanding on safety and hazards in various processes related to 3D printing, which include, but are not limited to, handling and process of 3D printing raw materials, building and removal of parts, and post processing of 3D printed parts. The typical safety and hazards concerns include emissions, laser or ultraviolet radiation, noise and ergonomic hazards, gas and material exposures, in particular nanomaterials. However, a comprehensive understanding on this important issue has been lacking.
In this project, the student will be working with Dr. Jing Shi on developing a methodology by using data mining tools to survey the current status on safety and hazards research of 3D printing. A critical analysis will also be conducted to illuminate the current gaps and future research directions. Dr. Jing Shi of MME department also serves as the deputy director of OSHE (Occupational Safety and Health Engineering) program under NIOSH Education and Resource Center at UC. The undergraduate students will have opportunity to learn data mining and visualization tools for literature survey, and perform the formal analysis, which is expected to lead to a peer reviewed research paper. The experience and skills to be learned can be applied to many other areas and problem settings. In addition, the students will not only be nurtured by the professor on a regular basis, but also have the opportunity to interact with the Ph.D. students in Dr. Shi’s research group.
Professor Murali Sundaram
Director – Micro and Nano Manufacturing Laboratory
Department of Mechanical and Material Engineering
631 Rhodes Hall
Cincinnati, OH 45221-0072
Tel: (513) 556-2791
Fax: (513) 556-3390
Email: murali.sundaram@uc.edu
Project Description
Electrical machining of insulators may seem like an oxymoron to many, but not for the researchers in the UC Micro and Nano Manufacturing Laboratory. Electrochemical discharge machining (ECDM) illustrated here is a non-conventional machining process that utilize an electric current to machine non-conductive material by this method. In this project, the student will use an existing setup (ECDM and high-speed camera) to capture the existing sparks and collect the data combining with existing codes to map the sparks.
Figure 1. In-house-built light detecting device.
Learning opportunities for students
As this research is multidisciplinary in nature, it offers tremendous opportunity for undergraduate students to be exposed to interdisciplinary research. The project will also introduce students to the various of academic research starting from literature review to report preparation. The experimentation involved will offer hands-on experience in research for the students. Students will learn about the theory behind the ECDM process and understand the working of the observing ECDM under a high-speed camera. The students will also be encouraged to present the work at either a conference and/or prepare a paper for journal publication.
Introduction and Motivation
Electrochemical Machining is a nontraditional manufacturing process that works on the principle of electrochemical dissolution of metal which is used for the production of components. There are several problems associated with the machining of titanium, one of which is Titanium forms an oxide layer (i.e., titanium dioxide), which is an obstacle to machining. It is present across metals, but especially pronounced in Titanium and its alloys. Titanium interacts with oxygen to form a native oxide film which protects metal from oxidation, the anodic polarization of titanium leads to the formation of the anodic oxide film and its thickening with increasing anodic potential in a wide range. Reaction for the same is given as:
Ti + 2H2O → TiO2 + 4H+ + 4e
This establishes the need to collect data in real time to track real time surface properties of base metal, Titanium and its oxide layer.
Project Scope and Goals :
In this project students will develop controls and sensor setup for data collection to track real time surface properties of Titanium, extending an already existing in-house ECM setup as shown in Fig[1]. Students will also work on cloud integration to store data, retrieve data, and generate analytics along with real time communication of analytics charts over email using AWS and Python
Sensors and Controls setup:
We are looking to track:
1) Real time changes in composition of electrolyte
2) Realtime images of titanium
3) pH level of electrolyte
4) Students are encouraged to do literature review and come up with more data points about surface properties of titanium which overlaps in ECM condition
To track above points, appropriate sensors and Arduino will be used to create control setup.
Fig[1] Inhouse setup of Electro-chemical Machining Process
Cloud integration:
1) Integrating AWS services like S3, Lexical and Alexa API to store and retrieve data.
2) Generating On - Demand analytics: Data stored in S3 will be queried using Lexical and Alexa API, and appreciate analytics will be generated using python as programming language which uses boto3 as sdk to interact with AWS
3) Real Time communication of analytics via email using AWS SES (AWS Simple Email Service)
Learning opportunities for students
This project will provide exposure to interdisciplinary research in nontraditional manufacturing, Robotics, and data science. Students will learn about Electro chemical manufacturing process, Cloud services, Python Programming. Students will get hands-on experience of doing end to end research projects which involve literature review, presentation, and report writing.
Final deliverables will include:
● Sensor and controls setup
● Cloud integration and analytics charts of data obtained from sensor and controls
Students will gain exposure to:
● Electro Chemical Machining process, Robotics, Cloud Services like AWS, Python programming
● Conducting a literature review and developing thought processes about how to integrate different fields viz nontraditional manufacturing processes like Electrochemical Machining, Robotics and Cloud Computing.
● Hands-on experience with a Electro-chemical machining setup, AWS, Python, arduino
Relevant standards and codes
● Project is to be completed pursuant to relevant standards and codes.
Introduction and Motivation
Technology grows exponentially smaller over time to meet the increasing demands of performance and portability across various industries; these include medicine, consumer products, electronics, aerospace, automotive, defense, and many others. Such shifts in technology have been made possible by ongoing research on the harnessing of scientific phenomena to perform material addition, removal, and/or modification at increasingly small size scales. The mission of the UC Micro and Nano Manufacturing Laboratory (https://ceas.uc.edu/research/centers-labs/micro-and-nano-manufacturing-laboratory.html) is to expand the horizons of what is possible in manufacturing at these size scales by researching the relevant fundamental scientific phenomena that make these processes work. Examples of prior work can be seen in Figure 1.
Figure 1. Micro and nano manufacturing processes studied in the UCMAN laboratory
Electrochemical Additive Manufacturing
One of the processes being studied is electrochemical additive manufacturing (ECAM). ECAM is a novel, emerging method of additive manufacturing that uses localized electrochemical deposition (localized metal plating) between a tool and a substrate when they are sufficiently close together in a metal plating bath. A current spike through the electrochemical circuit occurs when the tool and deposit touch, indicating that the metal deposit has grown between the tool-substrate gap enough to touch the tool. When this feedback is combined with a positioning and control system, this becomes an additive manufacturing (3d printing) process capable of depositing 3d metal parts. A video can be seen online at https://www.youtube.com/watch?v=0efMAGZl9XI.
Project Scope
Interest in functional advanced metal alloy parts is on the rise across multiple industries. In principle, metal additive manufacturing can fabricate such parts. However, severe limitations are present in conventional directed energy deposition (DED) based methods, primarily due to thermal complications. ECAM, as a nonthermal process, has the potential to overcome such limitations and fabricate alloy parts of complex shapes and composition distributions. This allows for novel parts to be produced for varying applications. While the ECAM process has been extensively studied using a system of one or two metals, the ability to control functional properties, and use more metals, is relatively unexplored. Control of the process at this scale requires rigorous selection of input process parameters, study of their effect on microstructure/composition, and characterization of functional properties.
Figure 2. Tasks involved with the project
Project Goals
Experimental goals include:
- Determination of the effective process conditions in which to run deposition. This involves testing behavior under different chemical, electrical, and geometrical conditions.
- Designing a method of tool path planning to build a 3D CAD model – with functional material composition encoded – under a given set of process conditions.
- Evaluating the deposition behavior using in-process monitored signals and post-process imaging and characterization methods.
Learning opportunities for students
Participating in this project will expose the undergraduate student to hands-on, interdisciplinary research. Students will build have the opportunity to build rare and valuable skills in studying physical phenomena from first-principles, experimentation characterization methods, analog hardware design, and/or modeling of the process at the atomic scale. Fundamental research skills will be covered including literature review, presentation, and report writing. The undergraduate student will also be encouraged to begin building a professional body of research work by presenting the work at either a conference and/or preparing a paper for journal publication.
Final deliverables will include:
· Experimental proof-of-concept on student-determined CAD files
· Documentation on the problem-solving process to generate each shape
Students will gain exposure to:
· Providing new knowledge on an emerging manufacturing technique
· Conducting a literature review
· Hands-on experiments with an electrochemical setup and hardware
· Coding of tool path planning algorithms and microprocessor control operations
· Problem solving
· An excellent opportunity to exercise your initiative, creativity, critical thinking, scientific judgment, scientific knowledge, problem solving, and teamwork skills
Relevant standards and codes
· Project is to be completed pursuant to relevant standards and codes.
Electrical machining of insulators may seem like an oxymoron to many, but not for the researchers in the UC Micro and Nano Manufacturing Laboratory. Electrochemical discharge deposition process is illustrated here is a non-conventional machining process that utilizes an electric current to deposit materials by this method. In this project, the student will use an existing electrochemical machining (ECDM) setup to try to deposit metal powders on a non-conducive glass workpiece.
Learning opportunities for students
As this research is multidisciplinary in nature, it offers tremendous opportunity for undergraduate students to be exposed to interdisciplinary research. The project will also introduce students to the various of academic research starting from literature review to report preparation. The experimentation involved will offer hands-on experience in research for the students. Students will learn about the theory behind the additive manufacturing and ECDM process and understand the working of the metal deposition. The students will also be encouraged to present the work at either a conference and/or prepare a paper for journal publication.
A current barrier to facilitating early tracheotomy is operating room access limitations and patient transportation challenges in ICU patients. Effectively transitioning tracheostomy from an operating room procedure to one readily completed in the Intensive Care Unit (ICU) or the Emergency Department or even in place of a cricothyrotomy by paramedics or first responders remains a technical challenge, and improper placement can be devastating. Percutaneous tracheotomy has grown in popularity as it can readily be performed at the bedside by an intensivist, obviating the need for a surgeon and/or valuable and limited operating room time; however, percutaneous tracheotomy is not appropriate in all patients, as those with morbid obesity, challenging neck anatomy from prior head and neck radiation or kyphosis, in need of an emergency airway, and on blood thinners are more suitable for open tracheotomy. To date, we have developed an artificial intelligence program capable of identifying space between tracheal rings more than 90% of the time that can reliably drive a needle into the airway in a semi-automated fashion in a cadaveric model. The objective of this proposal is to develop an Autonomous Ultrasound Robotic Assistance for Tracheotomy (AURA-Trach) with improved reliability, refined biomechanics, and enhanced outcomes by leveraging our current tracheostomy AI and ultrasound-guided miniature robotic prototype to allow accurate and reliable tracheotomy placement by a single person, securing a safe, patent airway. We hypothesize AI-assisted ultrasound can significantly improve the procedure guidance of percutaneous tracheotomy by reliably detecting critical anatomical landmarks around the neck across diverse populations, and miniature robotics can reduce the dexterity needed to safely place a tracheostomy tube by performing actuated needle, blade and dilator insertion. Specific opportunities on this project are improving ultrasounds-based AI algorithms, test model development, and mechanical testing.
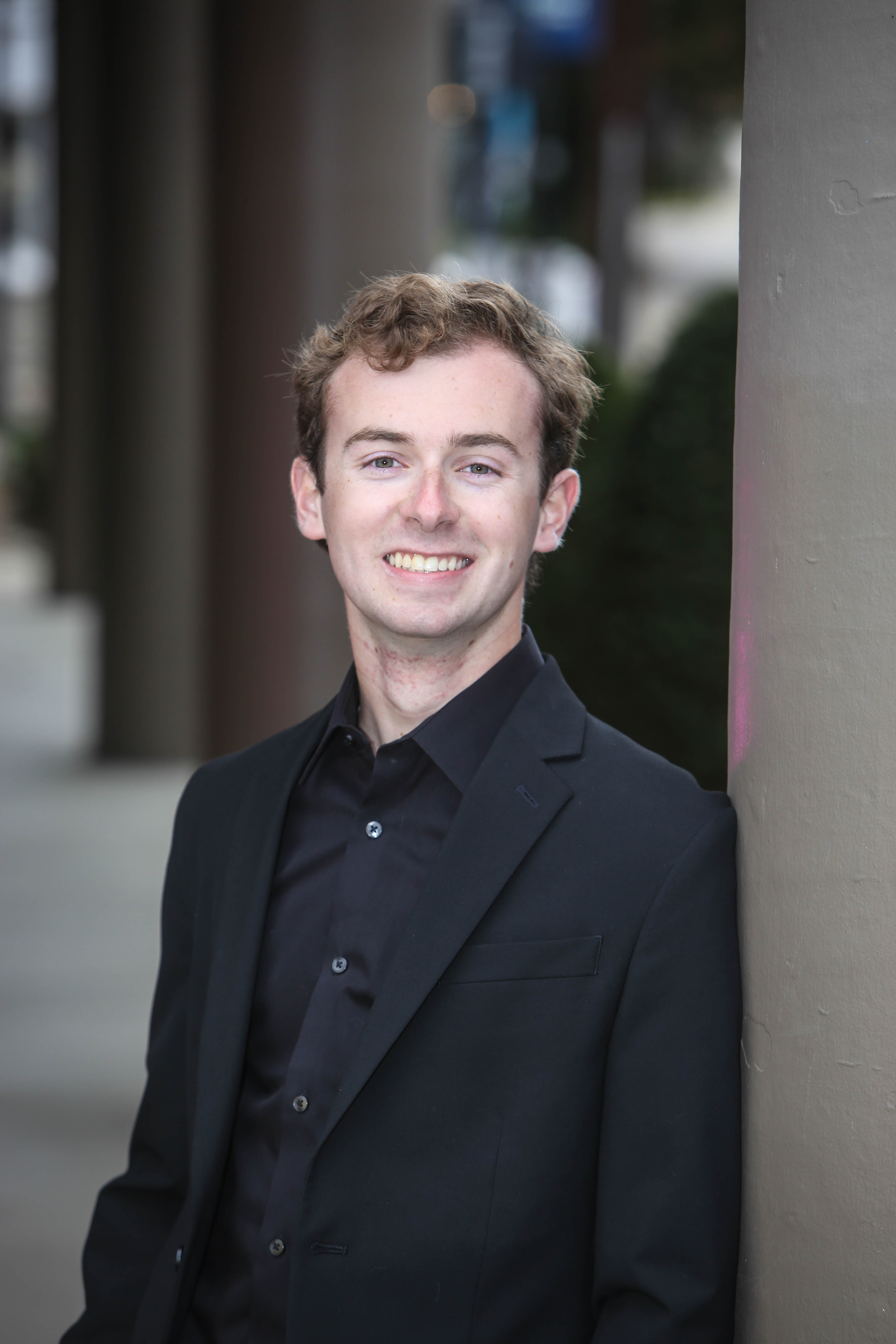
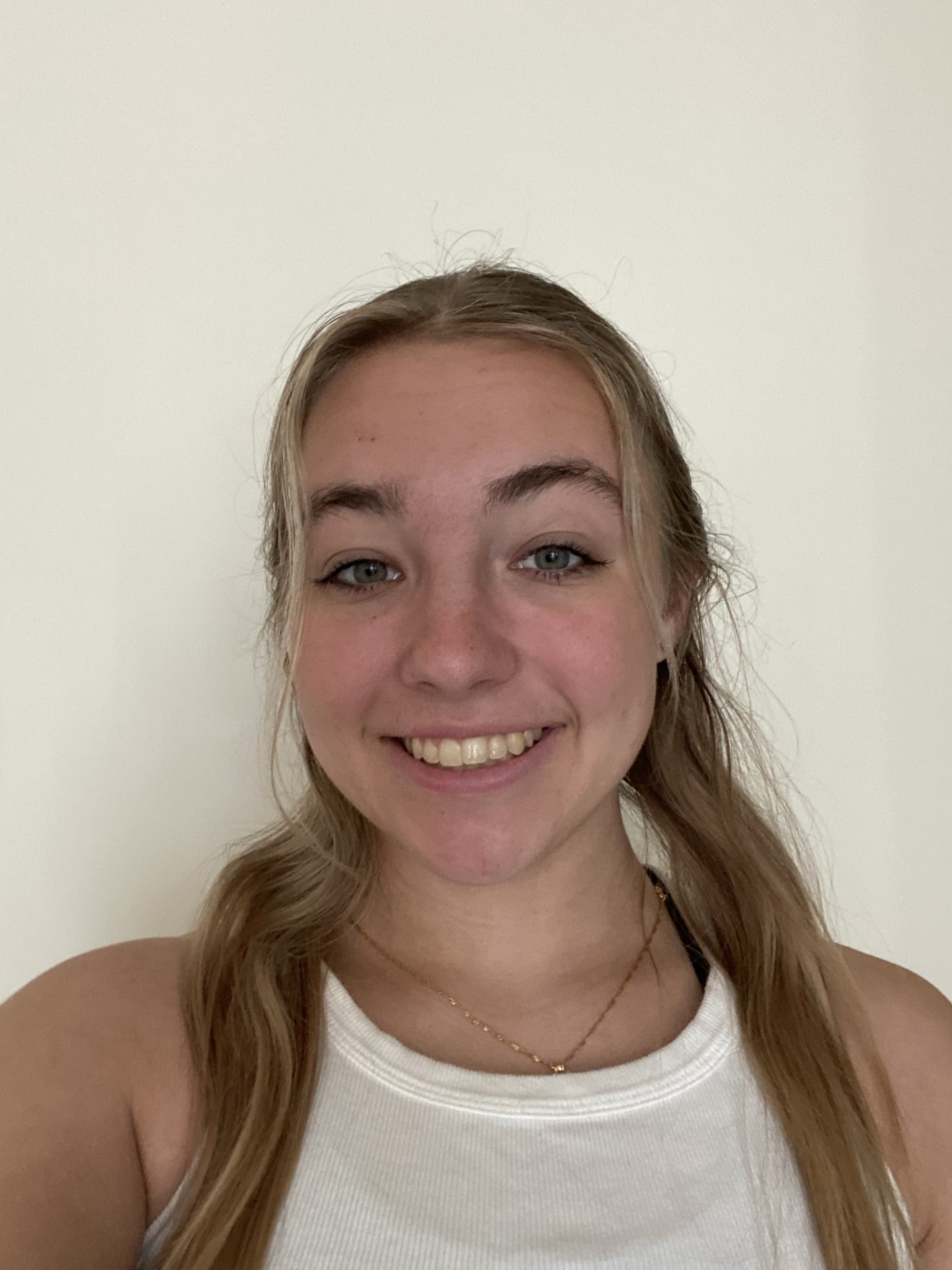
Left: Matthew Bish, advised by Manish Kumar, presented the telehealth drone.
Right: McKenzie Gatewood, advised by Rich Klaasen and Anjali Schrad of GE, presented the project Validation of Enhanced Ultrasonic Inspection Techniques for Improved Detection of Material Anomalies.
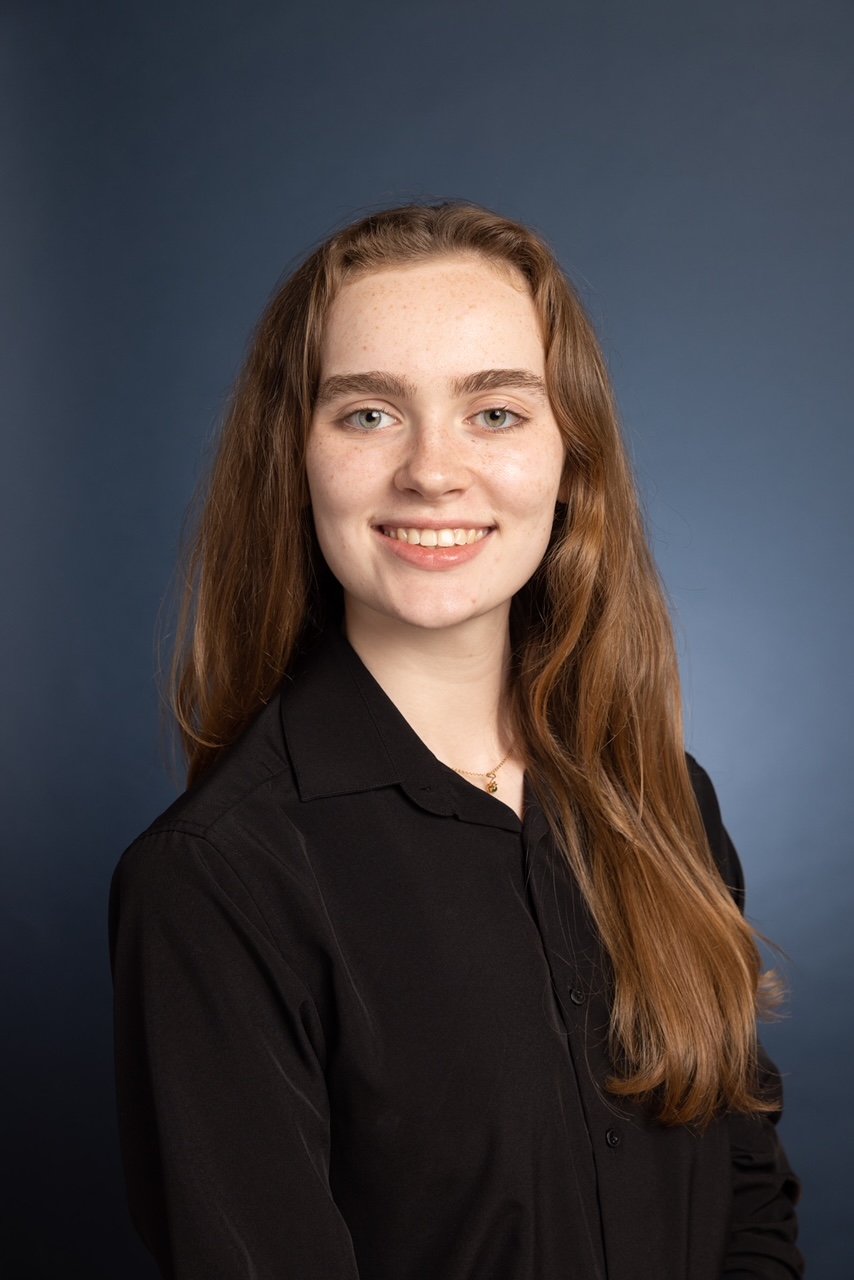
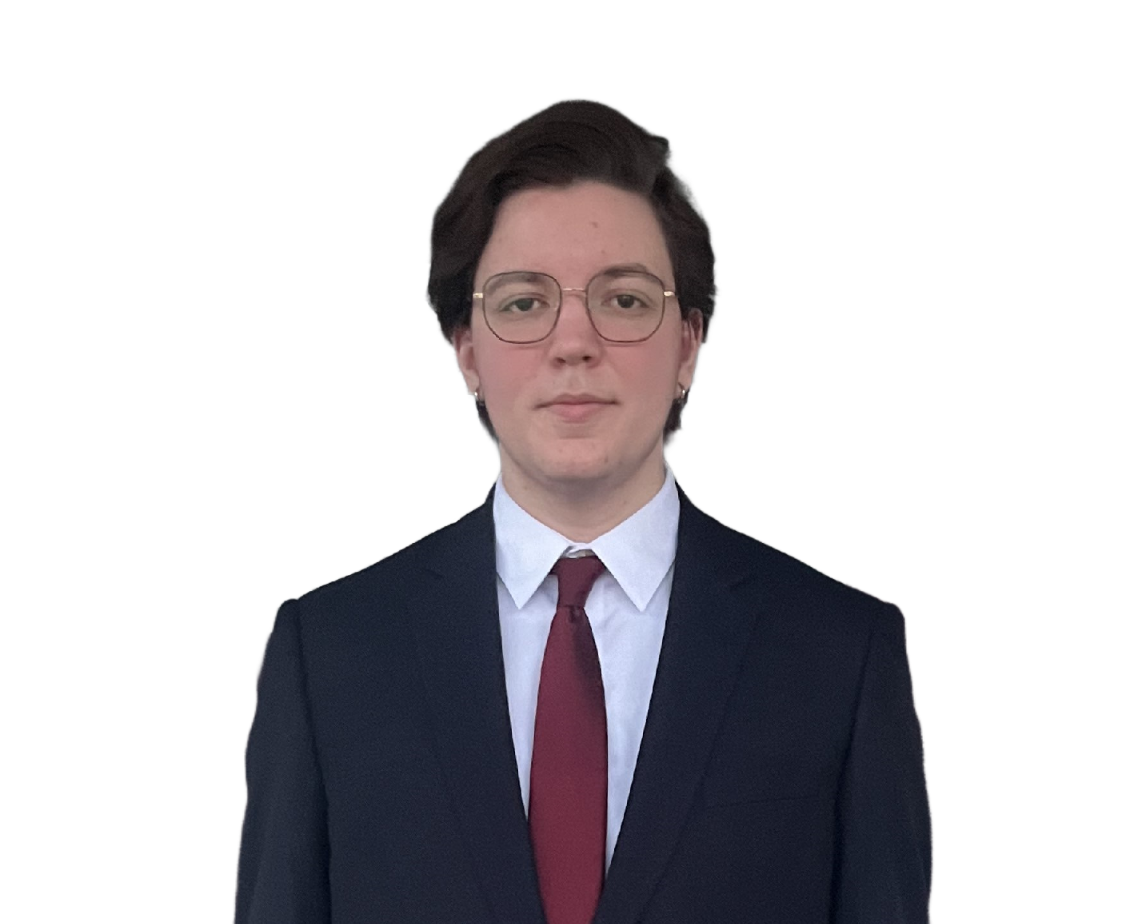
Left: Miriam Knutson, advised by Aashish Priye, presented the project Developing Inexpensive and Portable Molecular Diagnostics Tools for DNA Analysis.
Right: Owen Wilson, advised by Rashmi Jha, presented the project Neuromorphic Computing and Artificial Intelligence.
Left: Samarth Edlabakar, advised by Nan Niu, presented the project Exploiting Machine Learning to Solve the Next Release Problem. Center: Sarah Wessel, advised by Yoonjee Park, presented the project Long Term Dose-Controllable Drug Delivery. Right: Tristan Lopez, advised by Dan Cuppoletti, presented the project Boundary Layer Flow Control Research.
2023 Undergraduate Research Topics
Department | Research Area | Mentor | |
---|---|---|---|
Aerospace Engineering & Engineering Mechanics | Gas Dynamics and Propulsion Laboratory (Multiple Projects) | Ephraim J. Gutmark | |
Aerospace Engineering & Engineering Mechanics |
Fuzzy Logic-based Explainable AI | Kelly Cohen | |
Aerospace Engineering & Engineering Mechanics |
Aerospace Lab (Multiple Projects) | Daniel Cuppoletti | |
Chemical & Environmental Engineering | Developing Inexpensive and Portable Molecular Diagnostics Tools for DNA Analysis | Aashish Priye | |
Chemical & Environmental Engineering |
Tissue-Engineered Biomaterials for Nervous System Injury | Greg Harris | |
Biomedical Engineering | Injectable, Drug-coated Microparticles for Regenerating Bone Tissue | John Martin | |
Electrical & Computer Engineering | Testing Software Features with Requirements Knowledge | Nan Niu | |
Chemical & Environmental Engineering | Metabolomic Analysis of Butanol Production Under Stress | Maobing Tu | |
Chemical & Environmental Engineering | Long-term dose-controllable drug delivery | Yoonjee Park | |
Mechanical & Materials Engineering | Micro & Nano Lab (Multiple Projects) | Murali Sundaram | |
Mechanical & Materials Engineering | Fly a Drone Like a Kite | Manish Kumar | |
Electrical & Computer Engineering |
Microelectronics and Integrated-Systems with Neuro-centric Devices (MIND) Lab (Multiple Projects) | Rashmi Jha | |
Electrical & Computer Engineering | MEMS and Autonomous Integrated Microsystems Laboratory | Tao Li | |
Electrical & Computer Engineering; Physics | Superconducting Nanoelectronics with Perovskite Oxides | Marc Cahay & Evgeny Mikheev | |
Mechanical & Materials Engineering | Design of Alloys for the Hydrogen Economy | Eric Payton | |
Biomedical Engineering | Nebulized ECM Rescue Device (NERD) for Prehospital Use | Greg Dion | |
Biomedical Engineering | Wearable Health Sensors (Multiple Projects) | Orlando Hoilett | |
Biomedical Engineering | Effect of extracellular matrix composition on brain tumor resistance in a bioprinted glioblastoma model | Riccardo Barrile | |
Computer Science | Data Science to Analyze Biomedical Images (Multiple Projects) | Vikram Ravindra |
2022 Undergraduate Research Topics
Department | Research Area | Mentor | |
---|---|---|---|
Aerospace Engineering & Engineering Mechanics | Gas Dynamics and Propulsion Laboratory (Multiple Projects) | Ephraim J. Gutmark | |
Aerospace Engineering & Engineering Mechanics |
Fuzzy Logic based Flight Control of a Drone | Kelly Cohen | |
Aerospace Engineering & Engineering Mechanics |
Aeroacoustics of Electrically Propelled Air Vehicles (Multiple Projects) | Daniel Cuppoletti | |
Chemical & Environmental Engineering | Non-Contact Heating via Magnetic Eddy Current Heat Dissipation | Aashish Priye | |
Chemical & Environmental Engineering |
Tissue-Engineered Biomaterials for Nervous System Injury | Greg Harris | |
Biomedical Engineering | Injectable, calcium-scavenging hydrogels to prevent premature bone fusion | John Martin | |
Biomedical Engineering | Investigating the interactions of mechanical forces and hormones on ECM synthesis | Stacey Schutte | |
Electrical Engineering & Computer Science | Testing Software Features with Requirements Knowledge | Nan Niu | |
Electrical Engineering & Computer Science |
Learning Wing Motions in a Flapping-Wing Air Vehicle | John C. Gallagher | |
Chemical & Environmental Engineering | Innovative ways for removing PFAS in the environment | Maobing Tu | |
Chemical & Environmental Engineering | Long-term dose-controllable drug delivery | Yoonjee Park | |
Mechanical & Materials Engineering | Micro & Nano Lab (Multiple Projects) | Murali Sundaram | |
Mechanical & Materials Engineering | Telehealth Drones | Manish Kumar | |
Electrical Engineering & Computer Science |
Microelectronics and Integrated-Systems with Neuro-centric Devices (MIND) Lab (Multiple Projects) | Rashmi Jha | |
Electrical Engineering & Computer Science | MEMS and Autonomous Integrated Microsystems Laboratory (Multiple Projects) | Tao Li |
2021 Undergraduate Research Topics
Department | Research Area | Mentor |
---|---|---|
Aerospace Engineering & Engineering Mechanics | Aeroacoustics of Electrically Propelled Air Verhicles (4 projects) | Daniel Cuppoletti |
Aerospace Engineering & Engineering Mechanics |
Gas Dynamics and Propulsion Laboratory (GDPL) (8 projects) | Ephraim Gutmark |
Biomedical Engineering |
Engineering a Glioblastoma-on-Chip to Decipher the Contribution of Blood-Tumor-Barrier in Chemoresistance | Riccardo Barrile |
Biomedical Engineering | Investigating the Mechanisms behind Elastin Synthesis | Stacey Schutte |
Biomedical Engineering | Developing an Innervated Skin Model | Stacey Schutte |
Biomedical Engineering | Injectable, cell-degradable scaffolds for bone tissue engineering | John Martin |
Chemical & Environmental Engineering | Tissue-Engineered Biomaterials as a Solution to Peripheral Nervous System Injury | Greg Harris |
Chemical & Environmental Engineering | Replicating DNA in micro-sized convection cells | Aashish Priye |
Chemical & Environmental Engineering | Waste to Energy: Biofuels Production from Cellulosic Biomass | Maobing Tu |
Electrical Engineering & Computer Science | Simulation and Improvement of a Flapping-Wing Micro Air Vehicle | John Gallagher |
Electrical Engineering & Computer Science |
Microelectronics and Integrated-Systems with Neuro-centric Devices (MIND) Lab (2 projects) | Rashmi Jha |
Electrical Engineering & Computer Science |
Learning Environmental Assumptions via Natural Language Processing (NLP) | Nan Niu |
Electrical Engineering & Computer Science |
Microfluidic Devices with High Resolution and Aspect Ratio for Neural Circuitry Modeling (2 projects) | Tao Li |
Mechanical and Materials Engineering | Micro and Nano Lab (4 projects) | Murali Sundaram |
2020 Undergraduate Research Topics
Department | Research Area | Mentor |
---|---|---|
Aerospace Engineering & Engineering Mechanics | Aeroacoustics of Electrically Propelled Air Verhicles | Daniel Cuppoletti |
Aerospace Engineering & Engineering Mechanics | Advanced High-Speed Imaging Techniques for Future Propulsion Applications | Daniel Cuppoletti |
Aerospace Engineering & Engineering Mechanics | Active Flow Control for Aircraft Maneuvering and Control | Daniel Cuppoletti |
Chemical & Environmental Engineering | Real-time Aquatic Vertebrate Biosensor | David Wendell |
Chemical & Environmental Engineering | Waste to Energy: Biofuels Production from Cellulosic Biomass | Maobing Tu |
Electrical Engineering & Computer Science | Obfuscation Framework for Computer Hardware Design | Marty Emmert |
Mechanical & Materials Engineering | The Role of Microstructure on the Sensitization Response of 5XXX Series Aluminum Alloys | Matt Steiner |
Chemical & Environmental Engineering | Engineering Biomaterials to Direct Peripheral Nerve Regeneration | Greg Harris |
Electrical Engineering & Computer Science |
Pinball AI and Mechatronics | Zach Fuchs |
Mechanical & Materials Engineering |
Onboard Sense-and-Avoid (SAA) for small Unmanned Aerial Systems | Manish Kumar |
Aerospace Engineering & Engineering Mechanics |
Gas Dynamics and Propulsion Laboratory (GDPL) (8) Projects | Ephraim Gutmark |
Electrical Engineering & Computer Science |
Assessing Quality Attributes of Deep Learning Applications | Nan Niu |
Biomedical Engineering | Bioengineering a Blood-Brain-Barrier on-Chip to Investigate the Effect of Mechanical Shear Stress on Metastatic Invasion of the Brain | Riccardo Barrile |
Biomedical Engineering | 3D Bio-Printing of a Human Blood-Brain-Barrier-on-Chip for Modelling of Stroke | Riccardo Barrile |
Mechanical and Material Engineering | Non-traditional Method of Resin Reinforced Fiber Composite Machining | Murali Sundaram |
Mechanical and Material Engineering |
Scaling up of Electrochemical Additive Manufacturing | Murali Sundaram |
Mechanical and Material Engineering | Machining Non-Conductive Ceramics Using Pulse Electric Current | Murali Sundaram |
Mechanical and Material Engineering | Wire EDM | Murali Sundaram |
Mechanical and Material Engineering | Nanoscale Electrochemical Additive Manufacturing | Murali Sundaram |
Electrical Engineering & Computer Science |
Microelectronics and Integrated-Systems with Neuro-centric Devices (MIND) Lab | Rashmi Jha |
Chemical & Environmental Engineering | Controlling Drug Release | Yoonjee Park |
Electrical Engineering & Computer Science | Micromachined Chemical Sensor for Harsh Environments & Wireless Magnetoelastic Sensors for Implantable Biomedical Applications | Tao Li |
Chemical & Environmental Engineering | Replicating DNA in micro-sized convection cells | Aashish Priye |
Recent Research Archives
Other Archived Research Topics
Mark G. Turner
Professor, Aerospace Engineering Dept
mark.turner@uc.edu
An airfoil, compressor, fan and turbine design code has been developed at UC and made open source. Using analysis methods and optimization approaches, improved designs have been developed. A new airfoil developed this way for a wind turbine is shown in Fig. 1. Fig. 2 shows the fan geometry for a new electric propulsion application. This project will be to work with the geometry generator integrated with the optimization system to produce optimized blades for specified applications. In addition, the geometry generator has been integrated with an open source CAD package ESP developed at MIT and Syracuse University. It allows coupling with a lot of analysis software. The application of this tool will be developed further.
Mark G. Turner Professor
Aerospace Engineering Dept
mark.turner@uc.edu
The most common decelerator is a parachute. It is used for returning space capsules, mars missions, plane safety devices, paratroopers, and humanitarian air drops. The maple seed is nature’s perfect decelerator. See the figure below showing streamlines in the relative frame from a simulation of the maple seed using CFD by a UC MS student. A provisional patent has been issued for the ideas and further development is required. Funding for marketing of this device and some further prototype parts are available based on past protégé students’ presentations to the UC Commercialization office. It turns out that many aspects of a maple seed help improve its role to descend slowly. The protégé project will be:
- To test new concepts for uncontrolled designs and compare to models
- To further develop a controlled decelerator
- To integrate with concepts such as package delivery and rocket return
Greg M. Harris, Ph.D. Assistant Professor
Department of Chemical Engineering
Peripheral nerve injuries impact 1.4 million Americans each year with over 20 million people living with the effects of traumatic nerve injuries. In severe peripheral nerve injuries, nerve pathways, connections, and the extracellular matrix that lead to sensory or motor targets are disrupted. If the injury gap is over approximately 2 centimeters, functional recovery is extremely limited. This deeply impacts subsequent quality of life due to the loss of connections between the central nervous system and the body’s extremities. One primary reason for poor functional recoveries is that neurons do not have the proper guidance and signaling from the damaged extracellular matrix to allow targeted growth across the injured tissue. This project will address the urgent need to engineer bioactive materials to guide nerve regeneration to promote functional recoveries in traumatic nerve injuries. This will be accomplished by engineering polymers to possess the proper physical and chemical signals in order to direct cell and extracellular matrix alignment and growth. We will micropattern polymers to give alignment and combine the micropatterned polymers with a natural, extracellular matrix to facilitate regeneration and guidance of nerve. It is hypothesized that a bioactive, aligned polymer will functionally bridge the injury gap and guide neurons along scaffolds to restore function to the injured tissue.
Professor Maobing Tu
Department of Chemical and Environmental Engineering
tumg@uc.edu
Developing alternative biofuels from renewable biomass has great potential to reduce U.S. dependence on foreign oil while improving national energy security and addressing the environmental issues. The Renewable Fuel Standard mandates 36 billion gallons of biofuels should be produced annually by 2022, with 16 billion gallons coming from lignocellulosic biomass. Although ethanol has been the main candidate of transportation biofuels, butanol has several advantages over ethanol including low vapor pressure and tolerance to water contamination. Butanol is one of the promising advanced biofuels being pursued by the DOE, NSF and USDA for the next generation of alternative fuels. However, one of the major bottlenecks impeding production of viable biofuels from renewable biomass is the lack of cost-effective processes for converting biomass into biofuels including butanol.
Biomass pretreatment is needed to break down the recalcitrant structure of the plant cell wall for subsequent enzymatic hydrolysis and fermentation. However, the pretreatment processes generate inhibitors from the degradation of cellulose, hemicellulose, lignin and extractives, many of which significantly reduce the microbial growth and fermentation productivity during the fermentation process. Detoxification or conditioning methods are required to reduce the toxicity of hydrolysates for biofuels fermentation, but they increase the total production cost significantly. Progress has been made in the identification of hydrolysates inhibitors. However, the compounds identified to date cannot account for the inhibition level in real biomass hydrolysates and the most potent inhibitors remain elusive. Therefore, there is a critical need to better understand the chemistry of biomass-derived inhibitors with new approaches in the bioconversion processes. The protégé students will work on biomass pretreatment, enzymatic hydrolysis and butanol fermentation.
Dr. Lee
Chemical & Environmental Engineering
Project 1: Catalytic Elemental Mercury Oxidation
The U.S. EPA’s new final rule, Mercury and Air Toxics Standards, requires coal- and oil-fired power plants to use maximum available control technology to strictly regulate the emissions of mercury and other hazardous air pollutants by more than 90% effective in 2016. Among elemental, oxidized, and particulate-bound mercury species present in flue gas, elemental mercury vapor is most difficult to control because of its low concentrations, low reactivity, and low solubility in water. Elemental mercury vapor has a long residence time in the atmosphere, and thus contributes to global-scale deposition. Dr. Lee’s research group is studying detailed reaction mechanisms and kinetics responsible for the catalytic oxidation of elemental mercury vapor. He is also investigating the reaction and adsorption characteristics of elemental mercury vapor for a chemical adsorbent. A Protégé student will work with a PhD student on mechanistic and kinetic studies of elemental mercury over the catalysts.
Project 2: Energy-Efficient and Thermally Stable CO2 Adsorbent for Post-Combustion CO2 Capture
Post-combustion process in coal-fired power plants releases dilute carbon dioxide stream which is a major cause for increasing CO2 concentration in the atmosphere. As an increase in human activities, the CO2 concentration in atmosphere has reached 404 ppm in February 2016 that is reported to exceed a safe upper limit (350 ppm). This creates an expeditious need for suitable carbon capture and separation technology from existing coal-fired power plants. The flue gas from post combustion process consists of 10-16%(v) CO2. Conventional post-combustion CO2 capture processes using physical or chemical solvents require high regeneration energy of 3-4 MJ per kg of CO2 captured, thereby increasing an operating cost of the absorption process. Dr. Lee’s lab is studying CO2 adsorption process requiring very low adsorption and desorption energy requirements.
Project 3: Targeted and Controlled Gene and Drug Delivery for Cancer Therapeutics
The development of nano-scaled carriers as a drug delivery platform has made a tremendous difference in the fight against cancer. Significant progresses have been made in improving linker stability, biocompatibility, and biodegradability of a delivery system, targeting, and drug potency. Among many challenges, metastasis and multi-drug resistance phenomena still remain major challenges that limit the technological development of effective nanotechnology-based drug delivery systems. To address these technical challenges, Dr. Lee’s lab is developing a new class of smart gene and drug delivery systems with synergistic effect to target tumor and metastatic cancer cells. This novel nanoparticle-based delivery system has a few notable features of targeting to specific cells and sequential release of dual drugs for maximum efficacy. This new nanoparticle design can significantly reduce toxic side effects of conventional drugs used in chemotherapy by using ~100 times less amount of the conventional drugs.
Prof. Jingjie Wu
Chemical Engineering
jingjie.Wu@uc.edu
(513) 556-2756
593 ERC
The electrochemical conversion of carbon dioxide (CO2) into liquid fuels is a technology to recycle carbon while also storing intermittent renewable energy (e.g. wind and solar) into chemical energy (Figure 1). The advancement of this technology is currently limited by the lack of 1) efficient and stable catalysts, and 2) operative electrode architecture for solid-state electrochemical cell employment. The traditional metal catalysts require high overpotential (low energy efficiency) for the electrocatalytic CO2 reduction reaction (eCO2RR) due to the “linear scaling relationship” between reaction intermediates adsorption energy. More importantly they are deficient in C-C coupling to produce ethanol (C2H5OH). Additionally, they face a serious durability issue. The current electrochemical cell for eCO2RR includes a buffer layer through which liquid neutral or alkaline electrolyte flows.1 The involvement of liquid electrolyte not only results in large Ohmic loss but also causes extra cost in modular assembly.
This project dedicates to achieve direct eCO2RR to produce C2H5OH in a solid-state electrolyzer by realizing the following objectives: 1) develop carbon materials based catalysts through nanoscale design of topological structure; 2) maximize the triple-phase interface boundary in the catalyst layer by percolating theory; 3) design and manufacture a continuous flow solid-state electrolyze prototype by 3D printing. The refined electrochemical system targets eCO2RR into C2H5OH with a Faradaic efficiency (FE) of 90%, energy efficiency of 50%, current density 600 mA/cm2 , and 1000 h stability. The students will be involved in a multidisciplinary team to learn: catalysis, nanomaterials, 3D printing, and mass transport simulation by COMSOl.
Dr. Rashmi Jha, Associate Professor
EECS
Rashmi.jha@uc.edu
Primary Research Areas:
- Emerging Logic and Memory Devices beyond CMOS: Metal Oxide Semiconductor (CMOS) devices serve as the backbone of all processors and memory technologies. The continued scaling of CMOS devices, well known as Moore’s Law of Scaling, has instigated all major innovations in the areas of computing and data storage in the last few decades. The versatility of CMOS devices have also served as a launch pad for several new technologies ranging from smartphones, notebooks, tablets, and high performance computing, to MEMs technologies, and point of care devices. It is fascinating that CMOS devices today are as small as just 22 nm in gate length and semiconductor industry has roadmap for few mores generations of scaling the size of the transistor to around 5 nm by the year 2020. However, conventional scaling of Silicon based CMOS devices will approach fundamental limits and new technologies are needed to meet the computational demands of the future applications. My research group is focusing on emerging Logic and Memory devices that can address these bottlenecks. In particular, we are investigating transition metal oxide (TMO) based Resistive Random Access Memory (ReRAM) devices for high density data storage and in-memory computing architectures.
- Neuromorphic Devices and Computing: Albert Einstein famously said, “Look deep into nature, and then you will understand everything better”. A biological brain is an excellent computing machine. While today’s digital computers are extremely good at general purpose computing, they fail when it comes to solving a subjective computing problems. For example, a human brain can easily make decisions based on surrounding environmental conditions. A similar decision-making would be a daunting task for digital computers. Additionally, as CMOS devices are approaching their fundamental scaling limits, it becomes important to explore alternative ways of computing that are power efficient and scalable. To this end, people have traditionally explored Neural Networks. In fact, Deep Neural Networks (DNN) based machine learning is becoming increasingly important Developing brain inspired components such as neurons and synapses for cognitive computing. Image source: LinkedIn. Application of novel low-power data storage devices. Image source: Google IoT PoC Wearable electronics Smart phones Tablets Laptop Data storage Hardware Security ReRAM Devices Microelectronics and Integrated-Systems with Neuro-centric Devices (MIND) these days where cloud is getting inundated with massive amount of data generated by various sources. However, DNN still runs on digital computers that uses fundamentally different components and architecture than those found in a biological brain. Therefore, to address this challenge, our research group focuses on understanding the components and circuits in a biological brain and develops nanoelectronic neuromorphic devices and circuits that can match the energy-efficiency, scalability, and robustness of a biological brain for biomimetic learningbased computing and decision making. This research aligns closely with the recent grand challenge announcement from the White House in the areas of brain inspired computing.
For both projects, students will be involved in:
- Microfabrication of selector diodes in cleanroom.
- Testing of selector diodes on state of the art electrical testing equipment available in MIND lab at UC
- Data analysis and device modeling
- Working with Dr. Jha in a research of highly motivated graduate and undergraduate students.
- Exploration of Artificial Neural Network Circuits and interfacing with artificial synapses for Neuromorphic Architectures.
Professor Nan Niu
Department of Electrical Engineering and Computer Science
Software requirements traceability refers to “the ability to describe and follow the life of a requirement”. In modern software development such as agile and open-source projects, requirements are often represented in a lightweight way (e.g., modeled as user stories) and refined continuously. This research project aims to develop a new way of understanding the trace links by leveraging the rich repositories of issues, code commits, and their discussion from the project stakeholders. In particular, a heterogeneous graph of people, artifacts, and tasks will be developed, from which the traceability will be defined. The Protege student will join a team of graduate students in the Software Engineering Research Lab for the summer research, and the research results will be submitted for peer-reviewed publications.
Professor Murali Sundaram
Department of Mechanical and Materials Engineering
631 Rhodes Hall
Cincinnati, OH 45221-0072
(513) 556-2791
murali.sundaram@uc.edu
Project Description:
Background
While manufacturing processes improve, including the ever-popular emerging 3D printing process, a new issue arises – how do we deal with the material waste and pollution that results from the chemical processes to make products, the gases released in transportation, excess material not used in the process, or material from disposed products? Ventures such as Growduce have made new sustainable processes where food waste can be used to make products in your own home, eliminating the need for transportation or large manufacturing facilities. The food waste is placed into 3D printed plastic molds, where it dries out into a sterile and leathery material and can be used as an alternative to conventional plastic products, such as tableware or gloves. However, this process is still limited to using plastic for the template (manufactured using either 3D printing or a different process) for the food scraps to be molded in. This means that the previous issues of using non-biodegradable materials are still present. The goal of this project is two-fold: (1) to develop an extrusion-based 3D printing system that can directly print shapes out of biodegradable material without depending on an external mold or support system. This would require the students to design a way to store the biodegradable material and transport it to an extrusion system, as well as a timely way to solidify/dry the deposited material. (2) Then, to identify an item in daily life that could be made more sustainable by creating a biodegradable version, and use the system developed to print a functioning item that is biodegradable. The students will decide what parameters of the output part to evaluate and then test, re-design, and re-print as necessary. Some of the example parts under consideration are Gloves (Can they handle a task such as making a pizza or keeping your hands warm in the cold?) Shoes/Sandals – Can they withstand a walk from ERC circle to McMicken Commons? and Bags – What is the maximum weight it can withstand? For what amount of time until it breaks?
Learning opportunities for students
As this research is multidisciplinary in nature, it offers tremendous opportunity for undergraduate students to be exposed to interdisciplinary research. The project will also introduce students to the various aspects of academic research starting from literature review to report preparation. The simulation system development and experimentation involved will provide hands-on experience in research. Students will learn about 3D Printing, stepper motor control, use of biodegradable materials, and design of an extrusion system. The undergraduate student will also be encouraged to present the work at either a conference and/or prepare a paper for journal publication.
Professor Murali Sundaram Director
Micro and Nano Manufacturing Laboratory
Mechanical and Materials Engineering
631 Rhodes Hall
Cincinnati, OH 45221-0072
(513) 556-2791
murali.sundaram@uc.edu
Project Description
Material removal using high pressure water (water jet machining) is an emerging manufacturing method. Water jet machining has several applications in the biomedical and food processing industries due to its non-thermal nature, bio compatibility, and selective material removal. Hydro jet – a variant of water Jet machining is preferred during certain surgeries as the tumor may be selectively removed with minimal damage to surrounding blood vessels (ischemia) and veins. In food processing industry water jet cutting is preferred as it results in lower cross contamination when compared with traditional blade cutting. As part of the project the student will perform experiments using the custom built micro water jet system at the Micro and nano manufacturing lab. The student will also work with simulating the process to understand the machining characteristics of the process. Different work materials will be machined ranging from bio-materials to soft metals. Learning opportunities for students As this research is multidisciplinary in nature, it offers tremendous opportunity for undergraduate students to be exposed to interdisciplinary research. The project will also introduce students to the various aspects of academic research starting from literature review to report preparation. The experimentation involved will offer hands-on experience in research for the student. Students will learn about the theory behind the water jet machining process, and understand the workings of the water jet machine at the Micro and Nano Manufacturing Lab. Learn to use simulation software’s such as COMSOL, ANSYS and Matlab to interpret the findings of the theory. The undergraduate student will also be encouraged to present the work at either a conference and/or prepare a paper for journal publication.
Abstract: This project is to build and test a larger size prototype of a tiny medical robotic actuator or millirobot that has great flexibility and functionality, thus opening up a range of capabilities that are currently unavailable in medical or engineering areas. These millirobots will be a new paradigm for medical applications because they are larger than nanoparticle vehicles, which are too small to perform medical procedures, and smaller than the da Vinci Robot, which has centimeter-sized tools and arms that are too large to access many sites. Long catheters are also available, but lack the combination of being small, steerable through tissue, and functional at their tips. Millirobots will move in tissues, and will be functional at the tip driven via hydraulic and electrical power. The robot will move through tissue minimally invasively. Unique Aspects: Medical and engineering teams worldwide have sought to design miniaturized devices that can be directed to specific remote and otherwise inaccessible sites and then perform a series of tasks. Just as laparoscopic and catheter-based interventions have revolutionized medicine, millirobots would lay the groundwork for another revolution in precision medicine. One application is for cancer diagnosis and therapy. Some tumors are considered unresectable (inoperable, cannot be removed completely through surgery) if they’re located for example in critical areas of the brain, where surgical removal would be too dangerous or cause too much damage to healthy brain tissue. The millirobot may be used in these cases, Fig-1. The location of the tumor is one reason it may be inoperable. A tumor may be intertwined with blood vessels and other vital structures in the body making safe removal impossible. The millirobot may provide greater precision in surgery in these cases. Work Location: This research will be performed in the CEAS Nanoworld Laboratory in Rhodes Hall. Mark Schulz will be the mentor. Other faculty members may help guide the project. One or two students may work on this project. The project will be in an engineering lab, there will not be any medical work. Please contact Mark for a more detailed description of the project.
Mark J. Schulz, Professor and Co-Director of Nanoworld Laboratories
Mechanical & Materials Engineering
498 Rhodes Hall
Cincinnati, OH 45221
(513) 556-4132
mark.schulz@uc.edu
Dr. Vesselin Shanov Professor of Chemical Engineering Department of Chemical and Environmental
Office: 580 Engineering Research Center (ERC)
vesselin.shanov@uc.edu
(513)-556-2461
Graduate students will be also involved
Projects: 1. Energy Storage Devices Based on Three Dimensional (3D) Graphene and Carbon Nanotubes (CNT): Case Supercapacitors and Lithium–Ion Batteries 2. Electro-chemical Sensors Based on 3D Graphene and Carbon Nanotubes.
Project Summary Related to Project 1.
The big idea for this project is the National Academy of Engineering Grand Challenge to “Make Solar Energy More Economical.” The fast development of renewable and sustainable energy techniques such as solar cells and wind turbines requires efficient energy storage systems to offset the fluctuations in power availability caused by clouds or varying winds. The central challenge or objective of this project is to develop technology to produce a seamless 3D graphene called a Graphene Pellet (GP) and Carbon Nanotube (CNT) structure that are synthesized through chemical vapor deposition (CVD) using inexpensive nickel powder as catalyst template [1, 2]. GP is an important new platform for fabricating high performance supercapacitors, which is the first application of GP we intend to pursue. GP possesses well-controlled pore size (~2 nm), high electrical conductivity (148 S/cm) and good electromechanical properties. After electrochemical coating with manganese dioxide (MnO2), the GP/MnO2 electrode shows specific and volumetric capacitance up to 415 F g-1 and 235 F cm-3 , respectively, with capacitance retention of 90% after 5000 charge-discharge cycles. Moreover, when GP/MnO2 electrode is assembled with GP/polypyrrole electrode, the fabricated full cell prototype (supercapacitor) shows a superior electrochemical performance with a maximum energy density of 22.3 Wh/kg, maximum power density of 16.4 kW/kg, and very good cycle life that was able to power a light emitting diode (LED). These performance characteristics compare favorably to existing supercapacitors.
What work needs to be conducted to achieve the objectives? This research answers the guiding question: How do we fabricate multiple supercapacitors and batteries with reproducible properties? To answer this guiding question, following 6 tasks are proposed to be undertaken:
- Purchase of commercially available housing of supercapacitors and batteries.
- Synthesis of 3D graphene.
- Manufacturing of the positive electrodes of the supercapacitors and batteries.
- Manufacturing of the negative electrodes of the supercapacitors and batteries.
- Assembling the supercapacitor and battery devices.
- Electrochemical testing the supercapacitor and battery devices.
What research facilities will be used to conduct the research? The Nanoworld Laboratory at University of Cincinnati (http://www.min.uc.edu/nanoworldsmart) will be used for the research projects. It is a College laboratory for material and device development, teaching, and demonstrations. Nanoworld is an internationally recognized laboratory for trailblazing and road mapping innovation, translating the discoveries to industry, and training a next generation workforce that will be in high-demand.
Four labs form the Nanoworld Labs at University of Cincinnati:
- NANOWORLD, Main Lab 414A, 414B & 413 Rhodes Hall, Ph. 513-556-4652
- Nanocomposite Materials and Characterization Labs, Rhodes 507 and Rhodes 506
- Substrates and Nanomaterials Processing Laboratory, 581 Engineering Research Center (ERC)
- Pilot Microfactory for Nanomedicine Devices Lab, 587 ERC
Nanoworld may be the largest nanotube research laboratory in an academic setting with three commercial nanotube reactors to synthesize nanotube materials and transition the processes to industry. Nanotube reactors are in continuous operation along with post-processing and characterization equipment. Magnesium (Mg) single crystal manufacturing and coating systems are also used for developing biodegradable implants. University of Cincinnati Nanoworld supports research for undergraduate and graduate students from across the university. Prof. Vesselin Shanov of the Department of Chemical and Environmental Engineering (DCEE) and Prof. Mark Schulz of the Department of Mechanical and Materials Engineering (DMME) direct the Nanoworld lab. Faculty members from across the University and from the UC College of Medicine collaborate with Nanoworld. The main nanotechnology research in Nanoworld is in the field of synthesis, processing and characterization of carbon nanostructured materials, fibers, metal nanowires, nanocomposites, smart structures, electromagnetic devices, and sensors. Nanoworld is also developing innovations in medicine including Mg materials for biodegradable implants, microsensors and devices for interventional cardiology and cancer, and smart biodegradable implants. Nanoworld is also comprehensively involved in education and is frequently used to host middle school and high school students along with their science teachers. Nanoworld leads teaching two undergraduate nanotechnology courses at University of Cincinnati and one graduate course. These courses use state-of-the-art instrumentation in Nanoworld to perform lab modules. Also, students from other courses tour Nanoworld and learn about nanotechnology, biodegradable metals, biosensors, biomedical devices, and other advanced topics. Undergraduate through Ph.D. students, post-doctoral fellows, faculty members, and industry collaborators all work together in Nanoworld. Hundreds of people visit Nanoworld each year. The faculty members affiliated with Nanoworld bring a great deal of expertise and time to mentoring the students to assure the education and research experience is successful.
Prof. Manish Kumar
UAV MASTER Lab
Unmanned Aerial Systems (s-UAS) have generated a lot of interest recently among the research community due to their potential to revolutionize some of the applications in civilian domain such as emergency management, law enforcement, infrastructure inspection, precision agriculture, package delivery, and imaging/surveillance. Given these numerous potential applications and the inexpensive nature of these s-UAS, it is anticipated that there will be an extremely large number of UAS flying in much crowded airspace once allowed by government regulation. This presents several challenges in safe operation of UAS in terms of management of their traffic so that a large number of UAS can be operated in a congested airspace such that the required separation is maintained between manned aircraft, UAS and other stationary ground obstacles. One of the aspects of safe operation of UAS is having the onboard Sense-and-Avoid capability that would allow the UAS to be able to detect other UAS (and other mobile or stationary obstacles) in the neighborhood and plan an escape route to avoid the collision. Detection is enabled by onboard sensors such as radar or vision/thermal camera, or via ADS-B that allows one UAS to communicate to the others in the neighborhood. Once detection has occurred, the UAS should obtain an escape route to avoid the collision. UAV MASTER Lab has built prototypes that has laser and vision sensors. This project will advance the capability by adding radar and ADS-B technology. This project will involve hands-on experience of working with different sensors, flight controllers and UAS platforms, and software development to process sensor data and plan escape routes.